watch while the distilling plants are in operation.
Different ships have different types of distilling plants,
but all of the daily distilling plant operating records
require practically the same data.
The information required by this record consists of
the following:
1. Temperature, pressure, vacuum, flow, chemical
analysis, and density data from various points in the
distilling plant
2. Scaling record for each evaporator unit, which
includes the date of the last scaling, the hours operated,
and the quantity of distilled water produced
3. Starting, stopping, and total operating time of
each evaporator and various auxiliary machinery parts,
such as air ejector and pumps
4. Remarks concerning the operation and
maintenance of the distilling plant for each watch of the
day
You must make accurate entries in the Distilling
Plant Operating Record! Accurate entries not only help
predict troubles but, should abnormal operating
conditions suddenly develop, aid in locating the sources
of trouble.
For other recommended miscellaneous records,
refer to NSTM, chapter 90.
DISPOSAL OF ENGINEERING RECORDS
AND REPORTS
Before you destroy any of the engineering
department records, study the Disposal of Navy and
Marine Corps Records, USN and USNS Vessels,
SECNAVINST P5212.5 (revised). This publication
provides the procedures for disposing of records. For
each department aboard the ship, these instructions list
the permanent records that must be kept and the
temporary records that may be disposed of according to
an established schedule.
Both the Engineering Log and Engineers Bell Book
must be preserved as permanent records on board ship
for a 3-year period unless they are requested by a naval
court or board, or by the Navy Department. In such case,
copies (preferably photostatic) of records that are sent
from the ship are certified by the engineer officer as
being true copies and are put in the ships files.
At regular intervals, such as each quarter, records
that are over 3 years old are destroyed. When a ship that
is less than 3 years old is decommissioned, the current
books are retained on board. If a ship is scrapped, the
current books are forwarded to the nearest Naval
Records Management Center.
All reports forwarded to, and received from,
NAVSEA or another superior command may be
destroyed when they are 2 years old, if they are no longer
required.
Finally, to control the volume of paper work, reports
should only be kept on board ship if they
1. are required,
2. serve a specific purpose, or
3. may provide repair personnel with information
not found in publications or manuals.
MEASURE PROGRAM
All equipment requiring calibration or servicing
should be maintained at maximum dependability. To
meet this requirement, the Chief of Naval Material
implemented the Metrology Automated System for
Uniform Recall and Reporting (MEASURE).
The MEASURE system is a tool for your use. It is
only as good as the information that you put into it.
Therefore, it is important that alI the information be
complete, legible, accurate, and consistent.
As an EN you will be required to read gauges to
determine if the equipment is operating properly. The
gauges must be calibrated periodically to assure their
accuracy. The MEASURE program provides this
calibration. In this section, we will discuss some of the
major parts of the MEASURE system.
METER CARD
The METER card is a five-part color-coded form to
which the equipment identification and receipt tag is
attached. It is filled out by either the customer or the
calibrating activity. You will have a METER card for
every item for which you are responsible that requires
calibration.
This card is used to record a calibration action, to
add or delete items from inventory, to reschedule
calibration, to transfer custody, or to record manhours
for a completed calibration.
The white copy of a completed METER card is sent
to the MEASURE Operational Control Center
(MOCC), where the information is keypunched into a
computer to update the MEASURE data base. The new
information is then printed on another METER card and
1-9
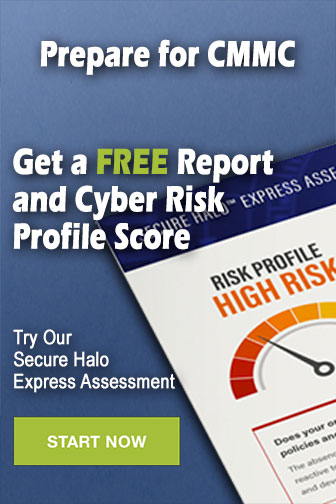