rapidly than a larger one, because the space available for
dirt accumulation is more limited. There are two
standardized sizes of fuel filter elements-large and
small. The small element is the same diameter as the
large but is only one-half as long. This construction
permits substitution of two small elements for one large
element.
You can increase the interval of time between
element changes by using the drain cocks on a filter
sump. Removal of dirt through the drain cock will make
room for more dirt to collect.
If new filter elements are not available for
replacement and the engine must be operated, you can
wash some types of totally clogged elements and get
limited additional service. This procedure is for
emergencies only. An engine must never be operated
unless all the fuel is filtered; therefore, a washed filter
is better than none at all.
Fuel must never flow from the supply tanks to the
nozzles without passing through all stages of filtration.
Strainers, as the primary stage in the fuel filtration
system, must be kept in good condition if sufficient fuel
is to flow in the system. Most strainers have a blade
mechanism that can be turned by hand. If you cannot
readily turn the scraper by hand, disassemble and clean
the strainer. This minor preventive maintenance will
prevent the scraping mechanism from breaking.
TRANSFER PUMPS.If the supply of fuel oil to
the system is to be maintained in an even and
uninterrupted flow, the fuel transfer pumps must
function properly. These pumps may become
inoperative or defective to the point that they fail to
discharge sufficient fuel for engine starting. Generally,
when a pump fails to operate, some parts have to be
replaced or reconditioned. For some types of pump, it is
customary to replace the entire unit. However, for worn
packing or seals, satisfactory repairs may be made. If
plunger-type pumps fail to operate because the valves
have become dirty, submerge and clean the pump in a
bath of diesel oil.
Repairs of fuel transfer pumps should be made
according to maintenance manuals supplied by the
individual pump manufacturers.
Malfunctioning of the Injection System
The fuel injection system is the most intricate of the
systems in a diesel engine. Since the function of an
injection system is to deliver fuel to the cylinder at a high
pressure, at the proper time, in the proper quantity, and
properly atomized, special care and precautions must be
taken in making adjustments and repairs.
HIGH-PRESSURE PUMP.-If a high-pressure
pump in a fuel injection system becomes inoperative, an
engine may fail to start. Information on the causes and
remedies for an inoperative pump can be found in the
manufacturers technical manual. Any ship using fuel
injection equipment should have available copies of the
applicable manufacturers technical manual.
TIMING.-Regardless of the installation or the type
of fuel injection system used, the timing of the injection
system must be correct to obtain maximum energy from
the fuel. Early or late injection timing may prevent an
engine from starting. Operation will be uneven and
vibration will be greater than usual.
If fuel enters a cylinder too early, detonation
generally occurs, causing the gas pressure to rise too
rapidly before the piston reaches top dead center. This
in turn causes a loss of power and high combustion
pressure. Low exhaust temperature may be an indication
that fuel injection is too early.
If fuel is injected too late in the engine cycle,
overheating, lowered firing pressure, smoky exhaust,
high exhaust temperature, or loss of power may occur.
Follow the instructions in the manufacturers
technical manual to correct an improperly timed
injection system.
Insufficient Compression
Proper compression pressures are essential if a
diesel engine is to operate satisfactorily. Insufficient
compression may cause an engine to fail to start. If you
suspect low pressure as the reason, check the
compression with the appropriate instrument. If the test
indicates pressures below standard, disassembly is
required for complete inspection and correction.
Inoperative Engine Governor
There are many troubles that may cause a governor
to become inoperative. The most frequent trouble
associated with starting an engine is generally caused by
bound control linkage or, if the governor is hydraulic,
by low oil level. Whether the governor is mechanical or
hydraulic, binding of linkage is generally due to
distorted, misaligned, defective, or dirty parts. If you
suspect binding, move the linkage and governor parts
by hand and check their movement. Eliminate any
undue stiffness or sluggishness in the movement of the
linkage.
3-29
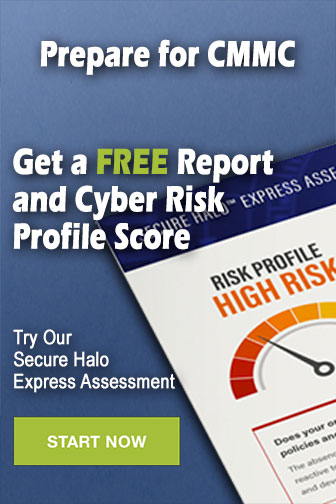