however, the permissible amount in each bin is usually
specified.
Daily visual inspection of the screens for cleanliness
is recommended, preferably before the start of
operation. When conditions warrant, the screens should
be cleaned.
NOTE: Always make sure the bolts securing the
screens are tight.
Hot Bins
Hot bins are used to store the heated and screened
aggregates temporarily in the various sizes required.
Each bin is an individual compartment or a segment of
a large compartment divided by partitions. A properly
sized hot-bin installation should be large enough to
prevent running out of material when the mixer is
operating at full capacity. Bin partitions should be tight,
free from holes, and of sufficient height to prevent
intermingling of the different size aggregates.
Hot bins usually have indicators that tell when the
aggregates fall below a certain level. These indicators
may be either electronic or mechanical. Each hot bin
should be equipped with an overflow pipe to prevent
excess amounts of aggregate from backing up into the
other bins. The overfill pipes should be set up to stop
overfilling of the bins. When a bin overfills, the screen
above the bin rides on the aggregate, resulting in heavy
carry-over and possible damage to the screen. Overflow
vents should be checked frequently to ensure they are
free flowing.
Sometimes, very fine aggregate particles build up
in the bin corners. When this buildup of aggregate
collapses, it can result in an excessive amount of fines
in the mix. This rush of fine materials normally occurs
when the aggregate in the bin is drawn down too low.
This condition can be controlled by having fillet plates
welded in the bin corners to eliminate the 90-degree
angles and by maintaining the proper aggregate level in
the bin.
Other potential obstacles to obtaining a good mix
includes a shortage of aggregate in one bin or excess in
another bin, worn gates (at the bottom of the bins) allow
leakage of aggregate, and sweating of the bin walls.
These obstacles must be overcome. Bin shortages or
excesses can be corrected by adjusting the cold feed.
Sweating occurs when moisture vapor in the aggregate
and in the air condenses on the bin walls. his usually
happens only at the beginning of the days operation or
when the coarse aggregate is not thoroughly dried.
Figure 8-11.-Segration of material in the bot bins.
Sweating may accumulate dust that, when released
suddenly, will add unwanted fines in the mix.
Hot-Bin Sampling
Most modern hot-mix asphalt plants are equipped
with devices for sampling hot aggregate from the bins.
These devices vary in design but usually serve to divert
the flow of aggregate from the feeders, or gates, under
the bins into sample containers. On continuous-flow
plants, the best place to obtain a sample is from the
feeder gates as the material is deposited onto the elevator
leading to the pugmill. Sampling facilities must be
constructed and located so that the samples obtained will
be representative of the material in the bins.
From the flow of aggregate over the screens, the
finer aggregates fall to the near side of the bins and
coarser aggregates fall to the far side (fig. 8-11). When
the aggregate is drawn from a bin by opening a gate at
the bottom, the flow of aggregate consists
predominantly of fine aggregate at one edge and coarse
aggregate at the other; therefore, the position of the
sampling device in the flow of aggregate determines
whether the sample will be composed of the fine portion,
the coarse portion, or will be an accurate representation
of all the aggregate in the bin. This condition is critical
in the bin that contains the fine aggregate since the
asphalt required in the mix is influenced heavily by the
aggregate from this bin.
Stratification (vertical layering) of sizes in the fine
bin may be caused by variation of grading in the
stockpiles or by erratic feeding of the cold aggregate.
When this form of segregation exists, representative
8-9
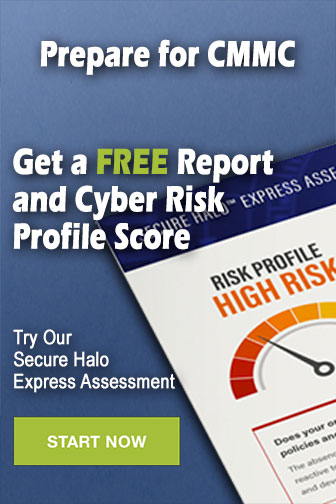