Compression ratio influences the thermal
efficiency of an engine. Theoretically, the ther-
mal efficiency increases as the compression ratio
is increased. The minimum value of a diesel engine
compression ratio is determined by the compres-
sion required for starting; and this compression
is, to a large extent, dependent on the type of fuel
used. The maximum value of the compression
ratio is not limited by the fuel used, but is limited
by the strength of the engine parts and the
allowable engine weight per bhp output.
Mechanical Efficiency
This is the rating that shows how much of the
power developed by the expansion of the gases
in the cylinder is actually delivered as useful
power. The factor which has the greatest effect
on mechanical efficiency is friction within the
engine. The friction between moving parts in an
engine remains practically constant throughout
the engines speed range. Therefore, the
mechanical efficiency of an engine will be highest
when the engine is running at the speed at which
maximum bhp is developed. Since power output
is bhp, and the maximum horsepower available
is ihp, then
bhp
Mechanical efficiency = ihp × 100
During the transmission of ihp through the
piston and connecting rod to the crankshaft, the
mechanical losses which occur may be due to fric-
tion, or they may be due to power absorbed. Fric-
tion losses occur because of friction in the various
bearings, between piston and piston rings, and
between piston rings and the cylinder walls. Power
is absorbed by valve and injection mechanisms,
and by various auxiliaries, such as the lubricating
oil and water circulating pumps and the scavenge
and supercharge blowers. As a result, the power
delivered to the crankshaft and available for
doing useful work (bhp) is less than indicated
power.
The mechanical losses which affect the effici-
ency of an engine may be called frictional
horsepower (fhp) or the difference between ihp
and bhp. The fhp of the engine used in
the preceding examples, then, would be
1343 (ihp) 900 (bhp) = 443 fhp, or 33% of
the ihp developed in the cylinders. Then, using
the expression for mechanical efficiency, the
percentage of power available at the shaft is com-
puted as follows:
900
Mechanical efficiency = 1343 = 0.67, or 67%
When an engine is operating under part load,
it has a lower mechanical efficiency than when
operating at full load. The explanation for this
is that most mechanical losses are almost indepen-
dent of the load, and therefore, when load
decreases, ihp decreases relatively less than bhp.
Mechanical efficiency becomes zero when an
engine operates at no load because then bhp = 0,
but ihp is not zero. In fact, if bhp is zero and the
expression for fhp is used, ihp is equal to fhp.
To show how mechanical efficiency is lower
at part load, assume the engine used in preceding
examples is operating at three-fourths load. Brake
horsepower at three-fourths load is 900 × 0.75
or 675. Assuming that fhp does not change with
load, fhp = 443. The ihp is, by expression, the
sum of bhp and fhp.
ihp = 675 + 443 = 1118
Mechanical efficiency = 675/1118 = 0.60, or
60%; this is appreciably lower than the 67%
indicated for the engine at full load.
Bmep is a useful concept when dealing with
mechanical efficiency. Bmep can be obtained if
the standard expression for computing
horsepower (ihp) is applied to bhp instead of ihp
and the mean pressure (p) is designated as bmep.
bhp =
(bmep) × L × A × N
33,000
or
33,000 × bhp
bmep = L × A × N
From the relations between bmep, bhp, ihp,
and mechanical efficiency, by designating
ENGINEMAN 1 & C
5-8
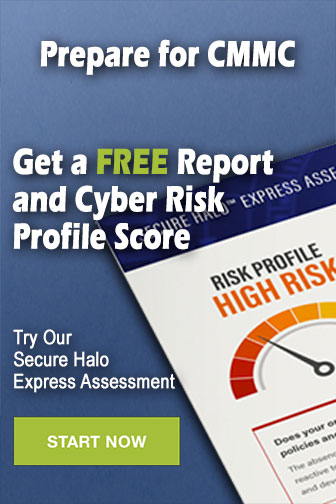