to the designated shop of the repair activity. After the
shaft has been repaired, or a new one has been made, it
is picked up and brought back to the ship by the ships
force. The pump is reassembled, inspected, and tested
by the ships force to make sure it is operating
satisfactorily.
An important thing to remember is that the repair
facility is responsible for ensuring that its personnel
repair or manufacture this this to the manufacturers
specifications, perform
all tests required by quality
assurance (QA), and fill out properly all the required
forms. You, however, are responsible for witnessing any
test required by QA, monitoring the status of the job at
all times, and reassembling and test operating the pump
properly. The end results will produce a reliable,
operating piece of equipment.
EQUIPMENT TESTS
As an EN2, you will assist in scheduling and
performing various tests on your equipment. The
purpose of those tests is to determine how your
equipment is performing and if there are any equipment
malfunctions. The tests are performed at various times,
such as (1) before the ship goes to the shipyard for
overhaul, (2) after post deployment, (3) during a tender
availability, or (4) as required by PMS. The tests are
performed by the ships force, IMA personnel, shipyard
personnel, or an inspection team (such as a Board of
Inspection and Survey [INSURV]). Detailed types of
inspections are described in COMNAVSURFLANT
Maintenance Manual, COMNAVSURFLANT INST.
9000.lC or COMNAVSURFPAC Ship and Craft
Maintenance Manual, Volumes 1 and 2, Planned
Maintenance, COMNAVSURPAC INST. 4700.lB.
Two types of inspections and tests that can be used
to spot impending trouble in an internal combustion
engine are called trend and spectrographic analyses. We
will now discuss and explain their importance and use
in detecting problems in internal combustion engines.
ENGINE TREND ANALYSIS
Preventive maintenance receives a great deal of
attention from everyone in the field of diesel engine
operation, since letting an engine run as long as it will
run and fixing it only after a breakdown occurs is not
only foolish, but extremely costly. On the other hand,
you would be just as foolish to constantly tear down an
engine just to inspect it. You should know that vital parts
of an engine last longer and operate better if they are not
tampered with unnecessarily. Therefore, an attempt
must be made to find a happy medium between these
two forms of maintenance.
One way to determine the condition of an engine is
by monitoring its operation. This is done by regularly
obtaining certain engine operating data and by studying,
analyzing, and comparing it with previous data. This
information is then reduced to a form that all
engineering personnel can interpret and decide whether
the engine needs to be overhauled or just temporarily
shut down for simple maintenance. For more detailed
p r o c e d u r e s , r e f e r t o N A V S E A S 9 2 3 3 - C 3 -
HBK-010/010, Diesel Engine, Over 400 BHP, Trend
Analysis Handbook
SPECTROGRAPHIC ANALYSIS
Spectrographic analysis is a method of determining
engine or equipment wear by analyzing engine oil and
hydraulic oil samples for chemicals and particles not
found in new oil or hydraulic fluid. This analysis is done
in laboratories on samples provided by ships according
to instructions given in their sampling kits.
Ships must maintain accurate records of operating
hours since major overhauls, oil changes, and samplings
to provide the testing facility with the information
requested in the sampling kit. (COMNAVSURFLANT
uses the services of the Charleston Naval Shipyard, and
COMNAVSURFPAC uses intermediate maintenance
activities (IMAs) for analyzing oil samples from
machinery employing closed lube oil/hydraulic
systems.) In addition, ships must maintain a record of
conditions found and repairs made as a result of
laboratory recommendations.
When the shipyard or IMA laboratory receives the
oil sample, a physical test and a spectrometric analysis
are performed. The physical test consists of the
following actions:
1. All samples are tested for fuel dilution, and a
report by percent volume is provided to all concerned.
1-19
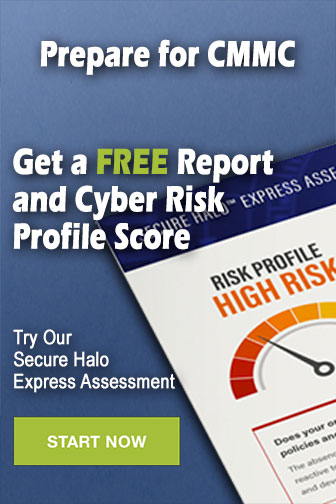