125 pounds per square inch (psi), the governor stops the
compressor from pumping air. When the tank pressure
falls to the cut-in pressure at about 100 psi, the governor
allows the compressor to start pumping again.
Air Storage Tanks
Air storage tanks (reservoirs) are used to hold
compressed air. The number and size of air tanks varies
among vehicles. The tanks hold enough air to allow the
brakes to be used several times, even if the compressor
stops working.
NOTE: Compressed air usually has some water and
some compressor oil in it which is bad for the air brake
system. For example, the water can freeze in cold
weather and cause brake failure. The water and oil tend
to collect in the bottom of the air tank; therefore, each
air tank is equipped with a drain valve in the bottom.
The two types of drain valves areas follows:
1. The manual valve shown in figure 3-45 is
operated by turning it a quarter turn or by pulling a cable.
Part of your post-operational procedures is to drain all
air tanks at the end of each day.
2. The automatic valve automatically expels the
water and oil. This system may also be equipped with a
manual drain.
Alcohol Evaporator
Some air brake systems have an alcohol evaporator
to put alcohol into the air system. This helps reduce the
risk of ice in air brake valves and other parts during cold
weather. Ice inside a brake system can make the brakes
stop working.
Figure 3-45.-Air tank manual drain valve.
If your vehicle has an alcohol system, the container
should be checked during each prestart operation and
filled up as necessary. Daily draining of the air tanks is
still required to get rid of the water and oil.
Safety Valve
A safety relief valve is installed in the first tank into
which the air compressor pumps air. The safety valve
protects the tank and the rest of the system from too
much pressure. The valve is usually set to open at 150
psi. If the safety valve has to release air pressure,
something is wrong in the air brake system. This should
be documented to inform the mechanic inspectors.
Brake Pedal
The brakes are applied by depressing the brake
pedal (also called the foot valve, or treadle valve)
that gives the operator control of the air brake
system. When the brake pedal is engaged, air from
the air tanks flows through the brake pedal valve
through the brake lines to the brake chambers close to
the wheel brakes that contain flexible diaphragms. The
force of the air admitted into these chambers causes the
diaphragms to operate the brake shoes through a
mechanical linkage.
Pushing the pedal down harder applies more air
pressure. Letting up on the brake pedal reduces the air
pressure and releases the brakes. Releasing the brakes
allows some compressed air out of the system; therefore,
the air pressure in the tanks is reduced and it must be
recharged by the air compressor. Pressing and releasing
the pedal unnecessarily may release air out faster than
the compressor can replace it, and should the pressure
become too low, the brakes cannot work properly and
brake failure will occur.
Pressure Gauge
An air pressure gauge lets you know if you have
proper air pressure within the reservoir. A low air
warning device should cut on before the pressure
drops to less than 60 psi in the air tank. This gauge is
usually on the instrument panel of a truck or bus. If the
pressure fails to buildup or exceeds the maximum limits
after building up, secure the truck until the fault is
corrected.
Hand Brake Valve
Independent control of brakes is necessary under
bad conditions, especially if you have to put on the
3-25
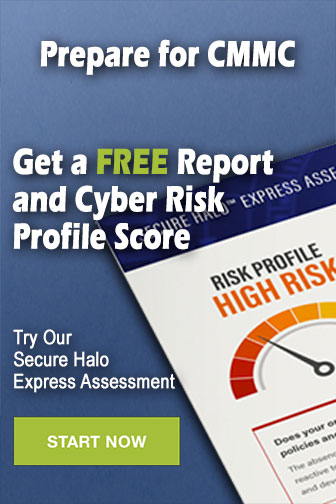