The steam, or pneumatic, hammer has basically
replaced the drop hammer. This hammer (fig. 12-60)
consists of a cylinder that contains a steam-driven or
air-driven ram. The ram consists of a piston equipped
with a striking head. The hammer is rested on the butt
or head of the pile for driving.
Figure 12-60. Steam, or pneumatic, pile hammer.
With a single-action steam, or pneumatic, hammer,
the power drive serves only to lift the ram; the
downward blow of the ram results from the force of
gravity only. In a double-action hammer, the ram is
both lifted and driven downward by the power drive. A
double-action hammer weighs from 5,000 to 14,000
pounds, and a single-action hammer weighs about
10,000 pounds.
The blows of the double-action hammer are lighter,
but more rapid than those of the single-action hammer.
The double-action hammer generally drives lightweight
or average weight piles into soils of average density.
The rapid blows tend to keep the pile in motion, thereby
reducing the resistance of inertia and friction. However,
when you are driving heavy piles in hard or dense soil,
the resistance from inertia and friction, together with the
rapid, high-velocity blows of the double-action hammer,
tends to damage the butt or head of the pile.
The single-action hammer is best for driving heavy
piles into hard or dense soil. The heavy ram, striking at
low velocity, allows more energy to be transferred into
the motion of the pile, thereby reducing impact and
damage to the butt or head of the pile.
A conventional pneumatic hammer requires a
600-cubic-foot-per-minute compressor to operate, and
the diesel is a self-contained unit constructed in sizes
that deliver up to 43,000 foot-pounds of energy per blow.
The diesel pile hammer is about twice as fast as a
conventional pneumatic, or steam, hammer of like size
and weight.
Diesel Hammer Operation
The most common diesel hammer used in the NCF
is the DE-10 McKiernan-Terry pile hammer shown in
figure 12-61. The hammer is lifted and started by a
single crane load line connected to a trip mechanism
(A). The hammer is started by lifting the ram piston (B)
with the load line until the trip mechanism (C)
automatically releases the ram piston. The ram piston
falls and actuates the cam of the fuel pump (D) that
delivers a measured amount of diesel fuel that falls into
a cup formed in the top of the anvil (E). Continuing its
downfall, the ram piston blocks the exhaust ports (F) and
begins compression of air trapped between the ram
piston and the anvil. The compression of the trapped air
creates a preloading force upon the anvil, the drive cap,
and the pile. The gravity propelled ram piston strikes
the anvil, delivering its impact energy to the pile.
The rounded end of the ram piston mates perfectly
with the cup in the anvil and displaces the fuel at the
12-42
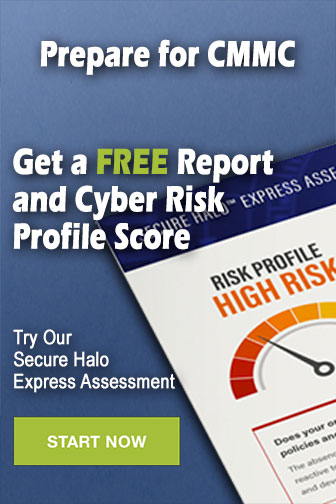