NAVAIR 01-1A-17 and NSTM, chapter 556,
provides information on low-lint wiping cloths.
Rust or corrosion initially present in a
hydraulic system can usually be traced to
improper storage of materials and component
parts. Particles can range in size from large flakes
to abrasives of microscopic dimensions. Proper
preservation of stored parts is helpful in elimi-
nating corrosion.
2. Particles introduced from outside sources.
Particles can be introduced into hydraulic systems
at points where either the liquid or certain working
parts of the system (for example, piston rods) are
at least in temporary contact with the atmosphere.
The most common contaminant introduction
areas are at the refill and breather openings,
cylinder rod packings, and open lines where
components are removed for repair or replace-
ment. Contamination arising from carelessness
during servicing operations is minimized by the
use of filters in the system fill lines and finger
strainers in the filler adapter of hydraulic
reservoirs.
Hydraulic cylinder piston rods
incorporate wiper rings and dust seals to prevent
the dust that settles on the piston rod during its
outward stroke from entering the system when the
piston rod retracts. Caps and plugs are available
and should be used to seal off the open lines when
a component is removed for repair or
replacement.
3. Particles created within the system during
operation. Contaminants created during system
operation are of two general typesmechanical
and chemical. Particles of a mechanical nature are
formed by wearing of parts in frictional contact,
such as pumps, cylinders, and packing gland
components. These wear particles can vary from
large chunks of packings down to steel shavings
that are too small to be trapped by filters.
The major source of chemical contami-
nants in hydraulic liquid is oxidation. These
contaminants are formed under high pressure and
temperatures and are promoted by the chemical
action of water and air and of metals like copper
and iron oxides. Liquid-oxidation products appear
initially as organic acids, asphaltines, gums,
and varnishessometimes combined with dust
particles as sludge. Liquid-soluble oxidation
products tend to increase liquid viscosity, while
insoluble types separate and form sediments,
especially on colder elements such as heat
exchanger coils.
Liquids containing antioxidants have little
tendency to form gums and sludge under normal
operating conditions. However, as the tempera-
ture increases, resistance to oxidation diminishes.
Hydraulic liquids that have been subjected to
excessively high temperatures (above 250°F for
most liquids) will break down, leaving minute
particles of asphaltines suspended in the liquids.
The liquid changes to brown in color and is
referred to as decomposed liquid. This explains
the importance of keeping the hydraulic liquid
temperature below specific levels.
The second contaminant-producing chemi-
cal action in hydraulic liquids is one that permits
these liquids to react with certain types of rubber.
This reaction causes structural changes in the
rubber, turning it brittle, and finally causing its
complete disintegration. For this reason, the
compatibility of system liquid with seals and hose
material is a very important factor.
4. Particles introduced by foreign liquids. One
of the most common foreign-fluid contaminants
is water, especially in hydraulic systems that
require petroleum-based liquids. Water, which
enters even the most carefully designed system by
condensation of atmospheric moisture, normally
settles to the bottom of the reservoir. Oil
movement in the reservoir disperses the water into
fine droplets, and agitation of the liquid in
the pump and in high-speed passages forms an
oil-water-air emulsion. This emulsion normally
separates during the rest period in the system
reservoir; but when fine dust and corrosion
particles are present, the emulsion is chemically
changed by high pressures into sludge. The
damaging action of sludge explains the need for
effective filtration, as well as the need for water
separation qualities in hydraulic liquids.
CONTAMINATION CONTROL
Maintaining hydraulic fluid within allowable
contamination limits for both water and particu-
late matter is crucial to the care and protection
of hydraulic equipment.
Filters (discussed in chapter 9) will provide
adequate control of the particular contamination
problem during all normal hydraulic system
operations if the filtration system is installed
properly and filter maintenance is performed
properly. Filter maintenance includes changing
elements at proper intervals. Control of the size
and amount of contamination entering the system
from any other source is the responsibility
3-9
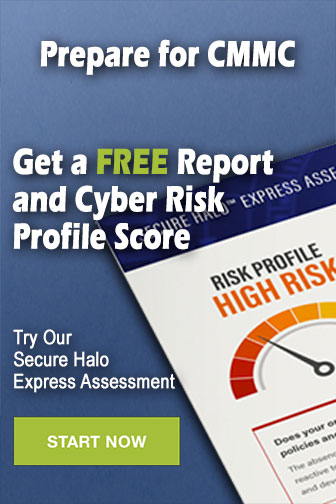