Measure the bore in the cylinder block, with a dial
indicating bore gauge, to determine if wear or an
out-of-round condition exceeds the manufacturers
specification. Figure 3-2 illustrates the use of a bore
gauge to measure a cylinder bore. You can use an inside
micrometer as well, but a dial indicating bore gauge is
easier to use.
Inspect and measure the engine blocks hold-down
bolt holes. Use a telescoping snap gauge to determine if
wear has caused enlargement of the holes. If a
telescoping snap gauge is not available, try to move each
bolt from side to side with your fingers. If a bolt moves
from side to side, its hole has enlarged and must be
repaired. Always follow the manufacturers instructions
on how to correct a hole enlargement problem.
DYE PENETRANT TEST
Conduct a preliminary dye penetrant test on the
engine blocks surface to identify cracks that you cannot
see otherwise. Be sure to follow the manufacturers
instructions on how to conduct this test. Remember that
only a certified nondestructive testing technician can
perform a dye penetrant test that meets the requirements
of quality assurance.
AIR AND WATER PRESSURE TESTS
Test the cylinder block for cracks in the cylinder
bores between the water jacket and the oil passages by
using either air pressure or water pressure. The purpose
of each test is to pressurize the water Jacket to the point,
within safe limits, that leaks show.
Figure 3-2.Checking the cylinder bore for wear or
out-of-roundness.
Air Pressure Test
Before you perform the air pressure test, make sure
you completely strip and clean the block. Then, follow
these basic procedures:
1. Seal all of the blocks freshwater passages with
gaskets and flanges.
2. Connect a low-pressure air hose to a fixture on
one of the flanges.
3. Immerse the block into a tank of water heated to
the engines normal operating temperature. Allow the
engine to soak for approximately 20 to 40 minutes, as
specified by the manufacturer. This allows the block to
warm to the temperature of the water.
4. Apply approximately 40 psi of pressure to the
block and watch for bubbles. Bubbles indicate a crack
or leak in the block. Determine what repair is needed or
can be made when you identify the source of the
bubbles.
If you cannot dip the block, you may still perform
the air pressure test. Attach the hose to a fixture secured
to an opening to the water jacket. Pressurize the water
jacket. Carefully spray soapy water over the block and
look for air bubbles caused by the pressurized air.
Water Pressure Test
The water pressure test is similar to the air pressure
test, except that defects are indicated by water leaks
rather than by air leaks. Before you perform the water
pressure test, strip and clean the block Then, follow
these procedures:
1. Seal off all but one of the freshwater openings
with flanges and gaskets. Make seals airtight.
2. Fill the water jacket with fresh water until all air
is purged from the water jacket. Seal the fill opening
with a flange that contains an air hose coupling.
3. Attach an air hose and pressurize the water
jacket to approximately 40 psi (see the manufacturers
manual). Maintain the pressure in the water jacket for at
least 2 hours.
4. Inspect the cylinder bores, air box, oil passages,
crankcase, and cylinder block exterior for the presence
of water. The presence of water at any of these locations
indicates that the water jacket has one or more defects.
3-2
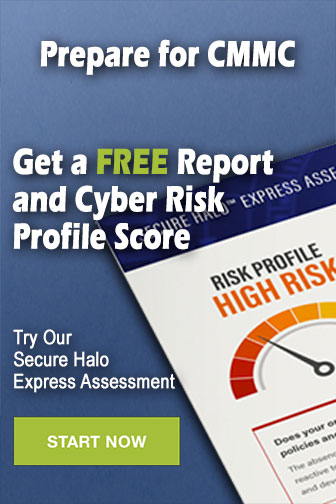