STANDBY PUMP.The standby pump is of
the same type as the main hydraulic pump, but
it is mounted at the forward end of the main
reduction gear housing and is driven through a
disconnect coupling. The suction strainer and suc-
tion gauge for this pump are mounted separately.
The primary function of the standby pump is to
assist the main pump in effecting pitch changes.
When the control pitch (C/P) unit is in the holding
pitch position, the standby pump discharge oil is
unloaded back to the sump through the hydraulic
block. But, whenever a pitch change is ordered,
the pump discharge oil is directed to the hydraulic
block high pressure passage.
LOWER OIL TANK.The lower (sump) oil
tank is usually located aft and below the OD box
assembly. The oil capacity of the sump varies
depending on the type and class of ship. Two
pumps, the main and standby hydraulic pumps,
take suction on the lower oil tank through a foot
valve, which permits the oil to flow from the tank
but does not allow it to return through the suc-
tion line.
UPPER GRAVITY OIL TANK.This tank
is located above the maximum draft line. Its main
purpose is to maintain hub oil pressure above that
of the surrounding seawater when the C/P unit
is secured. In the Kamewa installation, the
upper gravity oil tank serves an additional pur-
pose. During C/P unit operation the tank assists
in maintaining the sliding ring chamber pressure.
PRINCIPLES OF OPERATION
The CRP propeller provides the ahead and
astern propulsion thrust for a vessel by a change
in the pitch of the propeller blades. Such changes
can be obtained even when the main propulsion
machinery, including the propeller shaft, are
turning at a high rate of speed. Blade pitch con-
trol permits a full range of ahead and astern
thrusts. Maximum ahead thrust is provided with
the blades in the full ahead pitch position, and
maximum astern thrust is provided with the blades
in the full astern pitch position. When the pro-
peller blades are set at zero thrust, the propeller
shaft may be turning at any speed without im-
parting thrust to the vessel.
When a change of propeller pitch position is
ordered, a pitch position command from the pro-
pulsion control system is fed to the controls. This
command signal activates the electrohydraulic ser-
vocontrol valve which, in turn, activates the flow
of control oil to and from the OD box to change
the position of the valve rod actuator. The
hydraulic power oil flows to the OD box and is
admitted to the valve rod via the annular chamber
in the OD box and the ports in the valve rod. The
oil flows within the bore of the valve rod to the
hub servomotor, and returns from the hub via a
passage formed between the valve rod and the
propulsion shaft bore. The oil leaves the OD box
via ports in the OD box shaft and the annular
chamber to return to the sump tank. Control oil
is regulated by a set of sequencing and reducing
valves in the hydraulic system which maintain the
required pressure level. Control oil is supplied to
the electrohydraulic servocontrol valve. From the
servocontrol valve, the control oil flows to one
side of the low pressure (LP) chamber of the OD
box to drive the valve rod actuator. Control oil
returns to the sump through the OD box manifold
from the other side of the LP chamber.
When the propeller is operating at the desired
blade pitch position, the OD box valve rod
actuator is hydraulically locked and the hub ser-
vomotor is hydraulically held in a stationary posi-
tion. The configuration of the regulating valve pin
in the hub servomotor allows hydraulic power oil
to circulate continuously through the hub servo.
The oil pressure developed on each side of the hub
servomotor piston is balanced and established at
the level necessary to counteract blade loading
which would tend to change pitch position. A
hydraulic pitch change signal from the elec-
trohydraulic servo control valve moves the valve
rod actuator and the valve rod. This movement
changes the size of the oil passages to each face
of the hub servomotor piston, thereby creating
a differential pressure in the circulating oil to each
face of the piston. The regulating valve pin then
supplies high pressure oil to one face of the piston
and connects the other face to the return oil
passage. The high pressure oil develops the
necessary pressure on the piston face to overcome
blade loading and move the turning mechanism
and the blades to the desired pitch position. Blade
pitch will continue to change until the oil port
openings equalize and the oil pressure developed
ENGINEMAN 1 & C
4-14
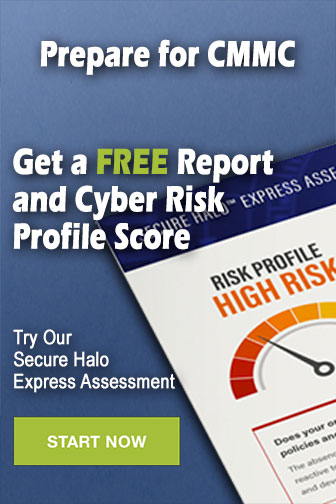