Chapter 4REDUCTION GEARS AND RELATED EQUIPMENT
from the shafting to the hub assembly. The hub
is secured to the tailshaft by flange bolts. These
bolts are not designed to take torque from the tail
shaft. The hub to tailshaft joint is sealed by
O-rings located between the hub and the tailshaft,
and between the tailshaft and the tailshaft spigot.
Each blade is attached to a crank pin ring by blade
bolts. The crank pin ring fits over and rotates
about a center post which is physically a part of
the hub body. The crank pin ring is retained in
the hub by the bearing ring. The area under each
blade is sealed by the blade port cover and by two
O-rings in the blade seal base ring. Each blade
seal base ring is spring-loaded against the under-
side of the blade port cover to provide a sealing
surface under all loading conditions.
The blade turning mechanism in the hub con-
sists of a single crosshead, attached to the end of
a piston rod. Several sliding blocks are fitted
into the machined chambers of the crosshead. An
eccentric pin on the underside of each crank pin
ring fits into a hole machined into each sliding
block. The hub servomotor is attached to the after
end of the crosshead. A piston rod carries the lines
for the regulating valve pin which is attached to
the end of the valve rod. This assembly forms a
passage for hydraulic power oil flow and return
oil flow to and from the hub.
class and DD 963 class ships, is mounted to the
forward end of the main reduction gear and is
flange-connected to the main reduction gear shaft
coupling. The other type, used on the LST
1179-1198 class ships, is called the Bird-Johnson
Kamewa Unit; it is manufactured of steel, is cast
in two sections, and is line-bored for installation
over the intermediate shaft. The OD box provides
a direct hydraulic oil connection to the main pro-
pulsion shaft and also translates to the valve rod
in response to hydraulic control oil commands.
High pressure oil from the hydraulic oil power
module (HOPM) is introduced through the OD
box to the internal bore of the valve rod and to
the hub. The oil returns from the propeller hub
to the hydraulic oil sump tank by way of the an-
nulus between the valve rod and the internal bore
of the shafting, through the OD box.
Hydraulic System
Valve Rod Assembly
The valve rod assembly is composed of
fabricated sections of seamless steel tubing
joined by couplings to provide a mechanical link
between the oil distribution (OD) box and the hub
servomotor through the internal bore of the
propeller shaft. The valve rod assembly provides
a passage for high pressure hydraulic oil from the
oil distribution box to the hub. Each valve sec-
tion is supported at the center of the propeller
shaft bore by guides. The after end of the valve
rod assembly supports a regulating valve pin
which operates in the valve pin liner of the hub
servomotor. The forward end of the valve rod
assembly is mechanically linked to the OD box
shaft, so that the valve rod assembly turns with
the shaft.
The hydraulic system consists of a self-
contained HOPM, a standby hydraulic pump
driven by the main reduction gear, the pitch con-
trol valves manifold block assembly, and all the
associated connecting piping, fittings, and valves.
The hydraulic oil is supplied to the hydraulic oil
pumps from a separate sump tank. To maintain
a static head pressure when the hydraulic system
is shut down, a gravity head tank is connected to
the OD box.
Oil Distribution Box
Presently there are two types of OD boxes
being used in the Navy. One type, used on FFG-7
HYDRAULIC OIL POWER MODULE.
The HOPM is located adjacent to the main reduc-
tion gear. It is a RESILIENT mounted, welded
structural assembly, consisting of a base plate with
structural ANGLE bar, flat bar, and mounting
plates. The HOPM contains the major com-
ponents of the hydraulic system, including (1)
either the motor-driven hydraulic screw or the
vane pump, coupling, and AC motor; (2) a suc-
tion strainer for the motor-driven pump; (3) two
40 micron duplex discharge filters; (4) the pressure
control assembly operating valves, which consist
of a pressure reducing valve, an auxiliary relief
valve, a check valve, an unloading and check
valve, and a relief and sequence valve; (5) one 10
micron duplex control oil filter; (6) a gauge panel
assembly and associated instrumentation; (7) a
manual bypass valve; and (8) the interconnecting
piping and fittings.
4-13
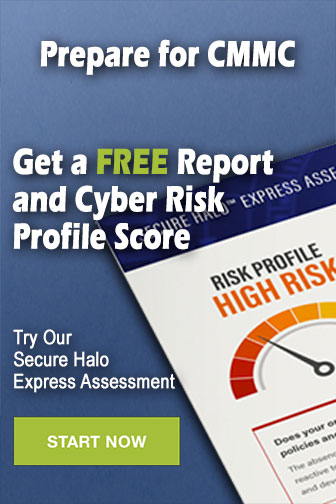