answer. In this way, the possible functional area of the
fault is progressively narrowed. Tolerance values are
presented in those instances where a definitive yes or no
is not obtained. This progression and elimination will
allow you to isolate the functional area of the equipment
containing the fault. After lessening the possible causes,
the diagram then refers you to the portion of the manual
needed to complete the fault isolation and repair. Each
diagram includes, or makes reference to, the
information necessary to establish the test or operating
conditions required for starting the fault isolation
procedure. The following three types of blocks are used
in fault logic diagrams.
Shaded blocks (right and bottom border lines
shaded) contain questions that may be answered from
observation, without changing the test setup and without
special equipment
Single-line blocks contain questions requiring
measurement by special setup of external test equipment
Double-line blocks (conclusion blocks) list the
fictional area within an equipment unit that is the
probable source of the malfunction and reference a
procedure or another diagram for further isolation or
correction of a fault
Functional Dependency Diagrams
The FDDs are used to support troubleshooting of
the gas turbine electronic power control system. An
FDD is a block diagram that illustrates the fictional
dependency of one test point (or circuit) upon another.
Signal Flow Diagram
The signal flow diagram depicts the circuitry for
each of the main functions of the circuit that you are
troubleshooting. The notes preceding the signal flow
diagram contain instructions for establishing operating
conditions and connecting test equipment that is
required for measuring the circuit parameters. For more
information on troubleshooting the LM2500, refer to
Propulsion Gas Turbine Module LM2500, volume 2,
part 1, NAVSEA S9234-AD-MMO-030/LM2500.
ECSS TROUBLESHOOTING
PROCEDURES
This section will provide you with some simple, but
helpful, information when isolating a fault in
engineering control and surveillance system (ECSS)
equipment. Remember, many of the tips previously
mentioned are still applicable for electrical/electronics
troubleshooting. To successfully troubleshoot any piece
of ECSS equipment, you should keep the following five
steps in mind:
1.
2.
3.
4.
5.
Energize the equipment to full operation using
the appropriate EOP steps and equipment
lineups.
Identify the faulting functional area.
Locate the test and signal flow diagram relating
to the faulting component.
Using the correct troubleshooting diagram,
isolate the malfunction to the faulting
replaceable or adjustable subassembly.
When a fault has been found to be in a specific
r e p l a c e a b l e s u b a s s e m b l y , r e f e r t o t h e
appropriate technical manual chapters for
connective maintenance instructions.
When using the signal flow diagrams for
troubleshooting, you should begin at the malfunctioning
component and work back to the original signal source.
By starting at the source of the problem, you should be
able to identify and correct the problem in an efficient
and timely manner.
TROUBLESHOOTING DIAGRAMS
The types of troubleshooting diagrams
used are the
and charts
signal flow diagrams (description is given in
previous section),
power distribution diagrams,
logic flow charts,
timing diagrams,
interconnecting diagrams,
troubleshooting functional dependency
diagrams, and
the circuit card locator and function information
plates.
Power Distribution Diagrams
Power distribution diagrams show the distribution
of the primary ac power, secondary ac power, and the
dc power from the input to the various components.
2-27
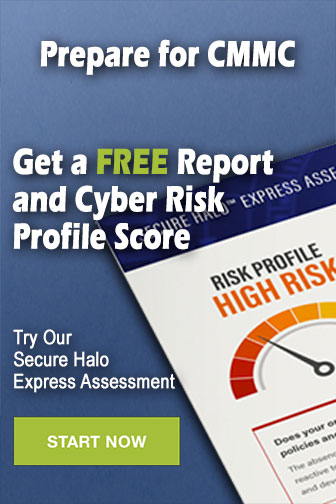