STRAINERS
Strainers are used primarily to catch only very
large particles and will be found in applications
where this type of protection is required. Most
hydraulic systems have a strainer in the reservoir
at the inlet to the suction line of the pump. A
strainer is used in lieu of a filter to reduce its
chance of being clogged and starving the pump.
However, since this strainer is located in the
reservoir, its maintenance is frequently neglected.
When heavy dirt and sludge accumulate on the
suction strainer, the pump soon begins to cavitate.
Pump failure follows quickly.
FILTERS
The most common device installed in
hydraulic systems to prevent foreign particles and
contamination from remaining in the system are
referred to as filters. They may be located in the
reservoir, in the return line, in the pressure line,
or in any other location in the system where the
designer of the system decides they are needed to
safeguard the system against impurities.
Filters are classified as full flow and
proportional or partial flow. In the full-flow type
of filter, all the fluid that enters the unit passes
through the filtering element, while in the
proportional-flow type, only a portion of the fluid
passes through the element.
Full-Flow Filter
The full-flow filter provides a positive filtering
action; however, it offers resistance to flow,
particularly when the element becomes dirty.
Hydraulic fluid enters the filter through the inlet
port in the body and flows around the filter
element inside the filter bowl. Filtering takes place
as the fluid passes through the filtering element
and into the hollow core, leaving the dirt and
impurities on the outside of the filter element.
The filtered fluid then flows from the hollow
core through the outlet port and into the system
(fig. 9-10).
Some full-flow filters are equipped with a
contamination indicator (fig. 9-11). These
indicators, also known as differential pressure
indicators, are available in three typesgauge
indicators, mechanical pop-up indicators, and
electrical with mechanical pop-up indicators. As
contaminating particles collect on the filter
element, the differential pressure across the
element increases. In some installations using
Figure 9-10.Full-flow hydraulic filter.
gauges as indicators, the differential pressure must
be obtained by subtracting the readings of two
gauges located somewhere along the filter inlet
and outlet piping. For pop-up indicators, when
the increase in pressure reaches a specific value,
an indicator (usually in the filter head) pops out,
signifying that the filter must be cleaned or
replaced. A low-temperature lockout feature is
installed in most pop-up types of contamination
indicators to eliminate the possibility of false
indications due to cold weather because the
pressure differential may be much higher with a
cold fluid due to increased viscosity.
Filter elements used in filters that have a
contamination indicator are not normally
removed or replaced until the indicator is
actuated. This decreases the possibility of system
contamination from outside sources due to
unnecessary handling.
The use of the nonbypassing type of filter
eliminates the possibility of contaminated fluid
bypassing the filter element and contaminating the
entire system. This type of filter will minimize the
necessity for flushing the entire system and lessen
the possibility of failure of pumps and other
components in the system.
A bypass relief valve is installed in some filters.
The bypass relief valve allows the fluid to bypass
the filter element and pass directly through the
outlet port in the event that the filter element
becomes clogged. These filters may or may not
be equipped with the contamination indicator.
Figure 9-11 shows a full-flow bypass-type
9-8
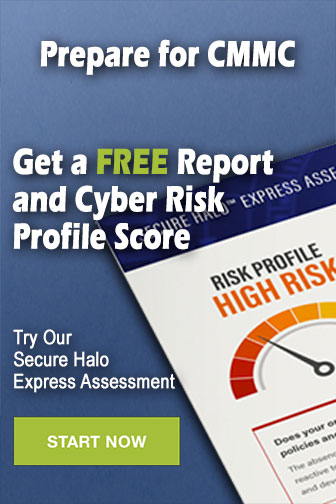