Wearfacing is commonly known in the NCF as
hardfacing. The purpose of hardfacing (fig. 5-15) is to
insulate many working parts of equipment from the
destructive forces that cause metal wear. The selection
of a hardfacing alloy for a certain application is based
on the capacity of the alloy to withstand or resist impact
and abrasion. Impact refers to a blow or series of blows
on a surface that results in a fracture or gradual
deterioration. Abrasion is the grinding action that results
when one surface slides, rolls, or rubs against another.
Under high compressive loads, this action can result in
gouging.
Alloys that resist abrasion well are poor in
withstanding impact, whereas those that withstand
impact well are poor in resisting abrasion; however,
there are many alloys whose hardfacing properties fall
between two extremes. These alloys offer some
protection against abrasion and withstand impact fairly
well. The hard-faced welding procedures, the type
material the part is manufactured from, and the primary
and alternate electrodes to perform the hardfacing
procedures are all outlined in NAVFAC P-433.
Hardfacing operations must be approved by the
maintenance supervisor.
Maintenance
Often, maintenance is put off to a later date because
of production. This may satisfy the immediate
production demands of the unit, but it is not good for the
equipment and creates a lax attitude toward scheduled
maintenance. When this occurs, a precedent is set that
leads to putting maintenance second to production.
Should this happen, it is not long before production rates
decline because of equipment breakdowns.
BLASTING OPERATIONS
Blasting operations are usually necessary when
working a quarry containing materials that cannot be
removed with construction equipment, such as front-end
loaders, bulldozers, and hauling equipment. Should this
be the case, blasting will come under the direct
supervision and control of a qualified blaster who carries
the NEC-5708. All other quarry personnel assigned
must follow written and oral instructions, carry out
assigned duties, and observe all safety precautions.
Limiting the number of personnel handling
explosives lessens the risk of accidents occurring. This
means one or two blasters have a definite assignment to
conduct several of the tasks involved in loading and
firing a blast. These tasks include the following:
carrying explosives and detonators, opening cases,
priming, loading, stemming, connecting blasting
circuits, and firing. The entire quarry crew must know
exactly what the blasters duties are. With such a system
observed, everything is accomplished in a precise and
orderly manner with no haphazard assumption of the
various tasks to be performed.
5-16
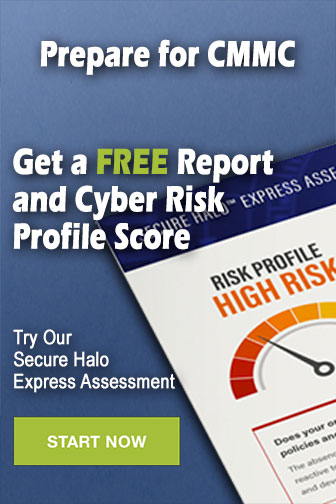