CHAPTER 1 GENERAL INFORMATION, EQUIPMENT DESCRIPTION, AND THEORY OF OPERATIONFIELD MAINTENANCE ENGINE GENERAL MAINTENANCECORROSION PREVENTION AND CONTROL (CPC) - ContinuedLIST OF ABBREVIATIONS/ACRONYMS - ContinuedLIST OF ABBREVIATIONS/ACRONYMS - ContinuedFIELD MAINTENANCE ENGINE EQUIPMENT DESCRIPTION AND DATAFigure 2. Propulsion Module.Figure 3. Diesel Engine External Components Top View.Figure 5. Diesel Engine External Components Starboard Side View.Figure 7. Diesel Engine External Components Aft View.Lubrication SystemFigure 8. Diesel Engine Internal Components.Table 1. Equipment Data.Table 1. Equipment Data - Continued.FIELD MAINTENANCE ENGINE THEORY OF OPERATIONFigure 1. Two-Cycle Sequence.Figure 2. Air Induction System.Figure 3. Turbocharger.Engine BlowerFigure 4. Fuel System.Figure 5. Fuel Injector.FUEL SYSTEM - ContinuedFigure 6. Fuel Pump.Figure 7. Cooling System.Figure 8. Water Pump.Heat ExchangerCoolant Filter and ConditionerLUBRICATION SYSTEM - ContinuedFigure 11. Oil Pump Gears.Figure 12. Oil Pump Pressure Regulator.Figure 13. Oil Cooler.Water-Cooled Exhaust ManifoldOverspeed GovernorCHAPTER 2 - TROUBLESHOOTING PROCEDURESTROUBLESHOOTING INDEXTROUBLESHOOTING PROCEDURES - ENGINE WILL NOT TURN OVERDefective engine start pushbutton.TROUBLESHOOTING PROCEDURES - ENGINE TURNS OVER BUT WILL NOT STARTWater in fuel/water separator.Fuel pump relief valve sticks open or partially open.The emergency air shutdown was activated.Replace starting motor (WP 0164).FIELD MAINTENANCE ENGINE TROUBLESHOOTING PROCEDURES - ENGINE DOES NOT START IN COLD TEMPERATURESTROUBLESHOOTING PROCEDURES - ENGINE STARTS WITH DIFFICULTY AND RUNS ROUGHWater is discovered in the fuel/water separator.Low compression.TROUBLESHOOTING PROCEDURES - SUDDEN LOSS OF POWERThe air inlet is blocked.TROUBLESHOOTING PROCEDURES - ENGINE LACKS POWERThe engine is not getting enough air.TROUBLESHOOTING PROCEDURES - ENGINE NOT RECEIVING FUEL FROM TANKLoose connections or cracked fuel lines.Power from diesel engine is lost and heavy black smoke is coming from exhaust plenum.TROUBLESHOOTING PROCEDURES - HIGH OIL CONSUMPTIONOverfilled crankcase.Turbocharger seals are leaking.Piston pin retainer loose.Dirt in air intake system.TROUBLESHOOTING PROCEDURES - LOW READING ON OIL PRESSURE GAUGEPoor circulation, oil cooler clogged.Electrical instrument panel sending units are faulty.TROUBLESHOOTING PROCEDURES - EXCESSIVE READING ON OIL PRESSURE GAUGECylinder blow-by, piston rings worn or broken.Faulty exhaust piping.TROUBLESHOOTING PROCEDURES - ABOVE NORMAL READING ON ENGINE COOLANT TEMPERATURE GAUGEFaulty thermostat.CORRECTIVE ACTION - ContinuedTROUBLESHOOTING PROCEDURES - BELOW NORMAL READING ON ENGINE COOLANT TEMPERATURE GAUGEBelow normal coolant temperature, excessive leakage at thermostat seal.TROUBLESHOOTING PROCEDURES - ENGINE FAILS TO STOP WHEN EMERGENCY STOP IS ACTIVATEDEmergency stop solenoid is defective.Fuel return line is clogged.TROUBLESHOOTING PROCEDURES - NOISY OPERATION OR VIBRATION IN TURBOCHARGERLeak in engine air intake piping and housing.TROUBLESHOOTING PROCEDURES - ELECTRICAL GENERATING SYSTEM SHOWS LOW BATTERY AND LOW OR NO CHARGING RATEDefective alternator.TROUBLESHOOTING PROCEDURES - ELECTRICAL GENERATING SYSTEM SHOWS FULLY CHARGED BATTERY AND HIGH CHARGING RATETROUBLESHOOTING PROCEDURES - ELECTRONIC GOVERNOR ACTUATOR STAYS AT MINIMUM POSITION WHEN POWER IS APPLIEDBinding electronic governor drive.ELECTRONIC GOVERNOR ACTUATOR STAYS AT MINIMUM POSITION WHEN POWER IS APPLIED - ContinuedELECTRONIC GOVERNOR ACTUATOR STAYS AT MINIMUM POSITION WHEN POWER IS APPLIED - ContinuedTROUBLESHOOTING PROCEDURES - ELECTRONIC GOVERNOR GOES TO FULL STROKE WHEN DC POWER IS APPLIED AND ENGINE IS NOT OPERATINGELECTRONIC GOVERNOR GOES TO FULL STROKE WHEN DC POWER IS APPLIED AND ENGINE IS NOT OPERATING - ContinuedFIELD MAINTENANCE ENGINE TROUBLESHOOTING PROCEDURES - FUEL SYSTEM TESTINGEngine runs rough/low on power.Figure 1. A3 Breaker Switch.PERFORM FUEL FLOW TEST - ContinuedPERFORM INJECTOR CUT OUT TEST - ContinuedPERFORM INJECTOR CUT OUT TEST - ContinuedFigure 4. Injector Manifold.PERFORM FUEL SPILL BACK TEMPERATURE TESTPERFORM FUEL SPILL BACK TEMPERATURE TEST - ContinuedFIELD MAINTENANCE ENGINE TROUBLESHOOTING PROCEDURES - FRESH WATER COOLING SYSTEM PRESSURE TESTINGFigure 1. Heat Exchanger Pressure Cap.Figure 2. Pressure Tester.FIELD MAINTENANCE ENGINE TROUBLESHOOTING PROCEDURES - FRESH WATER COOLING SYSTEM THERMOSTAT TESTINGTEST FRESH WATER COOLING SYSTEM THERMOSTAT - ContinuedTEST FRESH WATER COOLING SYSTEM THERMOSTAT - ContinuedCHAPTER 3 - MAINTENANCE INSTRUCTIONSFIELD MAINTENANCE ENGINE SERVICE UPON RECEIPTSERVICE UPON RECEIPT OF MATERIELFIELD MAINTENANCE ENGINE PREVENTIVE MAINTENANCE CHECKS AND SERVICES (PMCS) INTRODUCTIONCLEANING AND LUBRICATIONCORROSION PREVENTION AND CONTROL (CPC) - ContinuedFIELD MAINTENANCE ENGINE PREVENTIVE MAINTENANCE CHECKS AND SERVICES (PMCS), INCLUDING LUBRICATION INSTRUCTIONSTable 1. Preventive Maintenance Checks and Services for Engine - Continued.Table 1. Preventive Maintenance Checks and Services for Engine - Continued.PMCS Mandatory Replacement Parts ListSUSTAINMENT MAINTENANCE ENGINE PERFORM TUNE-UPFIELD MAINTENANCE ENGINE ENGINE MOUNTS INSPECTIONSUSTAINMENT MAINTENANCE ENGINE TESTINGPERFORM ENGINE COMPRESSION TEST - ContinuedPERFORM ENGINE COMPRESSION TEST - ContinuedPERFORM ENGINE COMPRESSION TEST - ContinuedFIELD MAINTENANCE ENGINE REPLACEMENTFigure 1. Fuel Supply and Return Valves Removal.Figure 3. Air Inlet Housing Removal.Figure 5. Engine Junction Box Removal.Figure 6. Fuel Supply Check Valve Removal.Figure 8. Gear Shifting Solenoids Removal.Figure 10. Raw Water Supply Hose Removal.Figure 12. Oil Filter Supply/Return Lines Removal.Figure 14. Marine Gear Mounting Bracket Removal.Figure 15. Forward Hull Saddle Removal.Figure 16. Engine/Marine Gear Removal.Figure 17. Marine Gear Removal.Figure 19. Engine/Marine Gear Installation.Figure 20. Forward Hull Saddle Installation.Figure 22. Lifting Brackets.Figure 24. Raw Water Hose Installation.Figure 26. Gear Shifting Solenoid Installation.Figure 28. Fuel Supply Check Valve Installation.Figure 30. Starter Solenoid and Alternator Installation.Figure 32. Fire Suppression System Installation.Install SINCGARS antenna (TM 11-5820-890-10-8).SUSTAINMENT MAINTENANCE ENGINE MAINTENANCE STAND INSTALLATION AND REMOVALConnect lifting slings and shackles to engine (Figure 1, Item 1).Figure 1. Engine Stand.SUSTAINMENT MAINTENANCE ENGINE ALIGNMENTFigure 1. Engine Alignment.Install transfer case to pump-jet machinery guard (TM 55-1945-205-10).SUSTAINMENT MAINTENANCE ENGINE AIR BOX TESTINGFigure 1. Air Box Check Valve.Start engine and warm up for five minutes (TM 55-1925-205-10).Figure 3. Air Box Drain Hose.Service cooling system (TM 55-1925-205-10).SUSTAINMENT MAINTENANCE ENGINE AIR BOX COVERS REPLACERemove marine gear cooler (TM 55-2040-211-24).Remove fuel system cooler (WP 0081).Coat seven hex head screws (Figure 1, Item 6) with antiseize compound.Perform operational checks (TM 55-1925-205-10).FIELD MAINTENANCE ENGINE AIR BOX DRAINS REPLACEMENTFigure 1. Air Box Drains Removal.Do not exceed 40 PSI (276 kPa) when using compressed air for drying componentsApply antiseize compound to all fitting threads.Install fuel system cooler (WP 0081).FIELD MAINTENANCE ENGINE AIR BOX DRAIN HOSE REPLACEMENTFigure 1. Air Box Drain Hose Replacement.Install fuel system cooler (WP 0081).SUSTAINMENT MAINTENANCE ENGINE REAR CYLINDER BLOCK PLATE REPAIRFigure 1. Cylinder Block Plate.SUSTAINMENT MAINTENANCE ENGINE REAR CYLINDER BLOCK PLATE REMOVAL AND INSTALLATIONFigure 1. Rear End Plate.Coat rear end plate (Figure 2, Item 4) and engine block (Figure 2, Item 1) with sealing compound.Using torque wrench, torque hex head screws (Figure 1, Item 10) to 420 in-lb (47 N·m).Install air box covers (WP 0036).SUSTAINMENT MAINTENANCE ENGINE FRONT CYLINDER BLOCK PLATE REMOVAL AND INSTALLATIONFigure 1. Cam Bearings.Figure 2. Front Block Plate Removal.Figure 4. Engine Block.Figure 5. Front Block Plate Installation.Install marine gear oil cooler (TM 55-2040-211-24).SUSTAINMENT MAINTENANCE ENGINE FRONT CYLINDER BLOCK PLATE REPAIRSupport cylinder block plate (Figure 1, Item 1) on a flat surface.SUSTAINMENT MAINTENANCE ENGINE BLOCK REPAIRExhaust manifolds removed. (WP 0157)33. Fresh water cooling system starboard thermostat housing removed. (WP 0140)59. Remove oil galley plugs (1, 2 and 3) from front of engine block (4).63. Remove two plugs (10) from right side of engine block (4).70. Remove reducing bushing (20) and ether starting aid thermostat (21).The plugs and dowels in the following steps should be removed only if damaged.86. Remove two dowels (46) from rear of engine block (4).Clean gasket material and sealant off engine block (4) surfaces using scraper.Inspect cylinder bore (51), grooves (52) and lands (53) for pitting and corrosion.Position C measurement shall not exceed 5.2180 in. (132.5372 mm). d.Counterbore depth at point A shall be between 0.4755 and 0.477 in. (12.13 and 12.12 mm) or between20. Remove hex head screws (55) and five main bearing caps (54).Coat core plug (34) threads with sealing compound.Coat oil galley plugs (38) threads with sealing compound.Install two dowels (43) in top of engine block (4) until they are flush.12. Coat three plugs (47) and two plugs (48) threads with pipe thread sealing compound.16. Install cup plug (49) on bottom of engine block (4).21. Torque plug (1) to 396-444 in. lbs (45-50 N-m) using torque wrench and socket set.25. Coat oil galley plug (3) threads with sealing compound.38. Torque plug (8) to 276-324 in. lbs (31-37 N-m) using torque wrench and socket set.43. Install two plugs (10) in right side of engine block (4).53. Coat oil galley plug (14) threads with sealing compound.66. Install two plugs (19) in left side of engine block (4).72. Torque plugs (22) to 228-264 in. lbs (26-30 N-m) using torque wrench and socket set.86. Coat elbow (27) threads with sealing compound.90. Coat two seal rings (57) with lubricating oil.94. Install eight compression gaskets (60).99. Torque engine block pressure test core plug to 230 270 ft lbs (311 366 N-m) using torque wrench.101. Add water until engine block water jacket is full.105. Apply 40 PSI of pressure to engine block (4) and maintain for at least two hours.112. Torque water inlet adaptor (36) to 230-250 ft lbs (311-339 N-m) using torque wrench.114. Remove eight compression gaskets (60) from cylinders (51).120. Coat engine block (4) with engine oil to prevent rust.22. Install fuel injector control tube. (WP 0086)49. Install starter motor. (WP 0164)SUSTAINMENT MAINTENANCE ENGINE CYLINDER HEAD POPPET VALVE ROCKER ARM COVERS REPLACEMENTThis task is typical for the replacement of poppet valve rocker arm covers on both port and starboard enginesFigure 1. Cylinder Head Poppet Valve Rocker Arm Covers.Install chain hook (Figure 1, Item 9) on strainer (Figure 1, Item 10).SUSTAINMENT MAINTENANCE ENGINE CYLINDER HEAD CRANKCASE BREATHER CLEANINGFigure 1. Engine Cylinder Head Crankcase Breathers.FOLLOW-ON MAINTENANCESUSTAINMENT MAINTENANCE ENGINE CYLINDER HEAD EXHAUST VALVES ADJUSTMENTFigure 2. Injector Follower.Figure 5. Push Rod Adjustment.Install cylinder head poppet valve rocker arm covers (WP 0044).CYLINDER HEAD REMOVAL AND INSTALLATIONLoosen four hose clamps (Figure 1, Item 3) from two fuel rod cover tube hoses (Figure 1, Item 4).Position wood wedges on bench for setting cylinder head (Figure 2, Item 11).Figure 3. Cylinder Head Gasket Removal.Attach lifting fixture (Figure 4, Item 10) to cylinder head and lift.Figure 4. Cylinder Block and Cylinder Head.Figure 5. Cylinder Head Bolt Torque Sequence.Figure 7. Fuel Rod Installation.Install operator's cab (TM 55-1925-205-23).REAR LIFTING BRACKETS REPLACEMENTFigure 1. Turbocharger Air Hoses Removal.Figure 2. Lifting Bracket.Figure 3. Turbocharger Air Hoses Installation.Perform operational check (TM 55-1925-205-10).CYLINDER HEAD POPPET VALVE ROCKER ARM REMOVAL, CLEANING, INSPECTION, AND INSTALLATIONRemove two brackets (Figure 1, Item 10) from cylinder head (Figure 1, Item 6).Figure 1. Rocker Arm Shaft Brackets.Wash rocker arms, shaft, brackets, and bolts with cleaning compound.Inspect rocker arm shaft brackets (Figure 1, Item10) for cracks. Install new bracket if damaged.SUSTAINMENT MAINTENANCE ENGINE CYLINDER HEAD POPPET VALVE ROCKER ARM REPAIRFigure 2. Rocker Arm Pin and Bushing Disassembly.Inspect clevis (Figure 2, Item 1) for damage. Discard defective part.Figure 3. Rocker Arm Pin and Bushing Assembly.SUSTAINMENT MAINTENANCE ENGINE CYLINDER HEAD FUEL MANIFOLD REMOVAL, CLEANING, INSPECTION, AND INSTALLATIONRemove metal tube assembly (Figure 1, Item 1).Figure 1. Cylinder Head Fuel Manifold.Install cylinder head poppet valve rocker arm cover (WP 0044).SUSTAINMENT MAINTENANCE ENGINE CYLINDER HEAD REPAIRFigure 1. Cylinder Head Disassembly.Figure 2. Cylinder Head Cleaning.Figure 3. Cylinder Head Inspection.Figure 4. Cam Follower Bore Inspection.Figure 5. Dummy Injectors in Cylinder Head.Figure 6. Cover Plates on Cylinder Head.Figure 7. Test Fixture Installation.Observe water tank for 20 minutes watching for bubbles indicating a leak or crack.Figure 8. Dummy Injector Removal.Figure 10. Cylinder Head Cover Plates.Install fuel system injector control tube (WP 0086).SUSTAINMENT MAINTENANCE ENGINE CYLINDER HEAD CAM FOLLOWER REPLACEMENTFigure 1. Cam Follower Removal.Remove cam follower (Figure 2, Item 4) from heated lubricating oil.Install cylinder head valve guide bridge (WP 0058).SUSTAINMENT MAINTENANCE ENGINE CYLINDER HEAD PUSH ROD REPLACEMENTRemove push rod (Figure 1, Item 3) assembly from cylinder head (Figure 1, Item 1).Install new retaining ring (Figure 1, Item 2) in cylinder head (Figure 1, Item 1).SUSTAINMENT MAINTENANCE ENGINE CYLINDER HEAD EXHAUST VALVE REMOVAL AND INSTALLATIONSupport cylinder head (Figure 1, Item 5), with bottom side down, on two wood blocks.Set cylinder head (Figure 1, Item 5) on its side.Figure 2. Valve Clearance.SUSTAINMENT MAINTENANCE ENGINE CYLINDER HEAD EXHAUST VALVE REPAIRFigure 1. Exhaust Valve Components.Figure 2. Exhaust Valve.Dispose of contaminated cloths in accordance with local procedures.SUSTAINMENT MAINTENANCE ENGINE CYLINDER HEAD EXHAUST VALVE SEAT INSERTS REPLACEMENTSupport cylinder head (Figure 1, Item 3) on two wooden wedges (Figure 1, Item 4).Figure 2. Lifting Fixture.Using replacing tool and hammer, drive inserts (Figure 1, Item 1) into cylinder head (Figure 1, Item 3).Install cylinder head exhaust valves (WP 0055).SUSTAINMENT MAINTENANCE ENGINE CYLINDER HEAD EXHAUST VALVE GUIDE BRIDGE REPLACEMENTFigure 2. Valve Guide Bridge.SUSTAINMENT MAINTENANCE ENGINE CYLINDER HEAD VALVE GUIDES AND SEALS REPLACEMENTFigure 1. Valve Guide Oil Seal.Place cylinder head (Figure 2, Item 1), bottom side up, on two wood wedges.Place cylinder head (Figure 3, Item 2), right side up, on arbor press.Install new valve guide oil seal (Figure 4, Item 1) as follows:Figure 4. Valve Guide Installation.SUSTAINMENT MAINTENANCE ENGINE CYLINDER HEAD EXHAUST VALVE GUIDES CLEANING AND INSPECTIONPlace cylinder head (Figure 1, Item 3) in cleaning tank filled with cleaning solution.Inspect valve guides (Figure 1, Item 2) for fractures, chipping, scoring or wear. Replaced damaged parts.SUSTAINMENT MAINTENANCE ENGINE CRANKSHAFT AND STABILIZER REMOVAL, CLEANING, INSPECTION, REPAIR, AND INSTALLATIONRemove hex bolts with washer (Figure 1, Item 3) from stabilizers (Figure 1, Item 1).Figure 1. Crankshaft, Bearings, and Stabilizer.Soak crankshaft (Figure 2, Item 6) in cleaning compound to remove dirt and oil.Figure 2. Crankshaft and Thrust Washer Surface Dimensions.Figure 3. Checking Crankshaft Bow.Figure 4. Crankshaft Journal Specifications.Figure 5. Crankshaft Woodruff Key and Plugs.Install the lower main bearing caps (Figure 6, Item 5) in their original locations.Figure 6. Crankshaft, Bearings, and Stabilizer.Figure 7. Crankshaft End Play.Figure 8. Crankshaft, Bearings, and Stabilizer.Figure 9. Checking Crankshaft Distortion.Install blower drive shaft (WP 0112).SUSTAINMENT MAINTENANCE ENGINE CRANKSHAFT REAR OIL SEAL REPLACEMENTLay flywheel housing (Figure 1, Item 1) engine side down on wooden blocks on workbench.Figure 2. Rear Crankshaft Oil Seal Installation.Install flywheel housing (WP 0072).SUSTAINMENT MAINTENANCE CAMSHAFT AND BEARINGS REPLACEMENTOn the rear of the engine, remove four screws (1), adaptor (2) and retainer (3) from left camshaft gear (4).Using puller J 24420, remove accessory drive pulley (14) from camshaft (10).Remove six intermediate bearing lock screws from camshafts.Only the left cam bearing has a gasket.Remove six lock rings and three intermediate cam bearing sets from camshafts.Install a new woodruff key (26) in the keyway on camshafts (10 and 11).Put six halves of intermediate bearings (30) onto the bearing journals of camshafts (10 and 11).2. Install the right-hand camshaft (11) into the engine block (21).Install six screws (19) and lock washers (20) into both rear bearings (27).14. On the front of engine, apply engine oil to both front cam bearing journals.20. Install woodruff key (15) into camshaft (10).27. Position two retainers (3 and 7) on cam shaft gears (4 and 8).33. Install fresh water cooling system pump drive gear. (WP 0148)50. Install cylinder head poppet valve rocker arms. (WP 0049)CAMSHAFT VIBRATION DAMPER REPLACEMENTFigure 1. Vibration Damper.Align woodruff key with woodruff key slot in camshaft.SUSTAINMENT MAINTENANCE CAMSHAFT GEARS REPLACEMENTRemove four cap screws (5), adaptor (6) and retainer (7) from left camshaft gear (8).Install the right-hand cam gear (8) onto the camshaft (11).Position two retainers (3, 7) on cam gears (4, 8).28. Install fuel cooler. (WP 0081)CAMSHAFT BALANCE WEIGHT REPLACEMENTFigure 1. Balance Weight.Install fresh water cooling system pump drive gear (WP 0148).CAMSHAFT ACCESSORY DRIVE PULLEY REPLACEMENTRemove woodruff key (Figure 1, Item 4) and discard.Figure 1. Accessory Drive Pulley.CAMSHAFT IDLER GEAR REMOVAL AND INSTALLATIONFigure 1. Gear Train.Place cleaning cloth between camshaft gears to stop gears from rotating.Install turbochargers (WP 0114).SUSTAINMENT MAINTENANCE CAMSHAFT IDLER GEAR REPAIRClean excess grease and oil from idler gear and hub assembly (3) with cleaner.Remove bearings (6) from idler gear (4).Inspect idler gear (4) for corrosion, pitting or cracking. Replace defective part.7. Position the other bearing cup, number side down, on the idler gear16. Install inner spacer (7) over hub (5).1. Mount idler gear and hub assembly (3) in vise by plate (11).Install retainer (2) on idler gear and hub assembly (3).ENGINE FLYWHEEL REPLACEMENTAttach engine and transmission lifting sling to flywheelCoat 10 flywheel bolts with antiseize compound.Figure 1. Flywheel Replacement.ENGINE FLYWHEEL REPAIRNote the direction of the chamfer on the ring gear.Figure 1. Flywheel.Using torch set and heat protective mittens, flash heat ring gear uniformly.FLYWHEEL HOUSING REPLACEMENTLube oil dipstick tube assembly removedInstall two lifting eye bolts in flywheel housing.Remove four cap screws and washers from flywheel housingRemove cap screw and copper washer.Remove gasket and discard.Remove two cap screws and lockwashers. Discard lockwashers.Remove cap screw from access hole.Remove gasket from engine rear end plate and discard.Remove lifting eye bolts from flywheel housingPolish end of crankshaft with abrasive cloth wet with engine lubricating oil.Coat threads on pipe plugs (Figure 13, Items 3 and 4) with pipe sealing compound,.Install new cap screw (Figure 16, Item 1) into access hole.Install two new cap screws and new lockwashers into flywheel housingInstall access plate (Figure 19, Item 4) on flywheel housing (Figure 19, Item 1).Install new gasket (Figure 20, Item 11) on flywheel housing (Figure 20, Item 3).Remove slings, shackles, two lifting eye bolts and four aligning studs from flywheel housingInstall six new cap screws and new lockwashers into flywheel housingFlywheel Tightening Sequence DiagramFlywheel Housing Torque Sequence DiagramApply ultra blue sealing compound to flywheel housing (Figure 29, Item 1) and to access coverInstall flywheel (WP 0071).Install crankcase breather limiter (WP 0106).PISTON AND LINER ASSEMBLY REMOVAL AND INSTALLATIONFigure 1. Oil Distribution Inlet Tube and Screen Assembly Removal.Figure 2. Piston and Air Inlet Ports.Figure 4. Connecting Rod Cap and Bearing Removal.Figure 6. Cylinder Liner Seal Rings Removal.Figure 7. Cylinder Liner Seal Rings Installation.Figure 8. Piston and Liner Installation.Figure 9. Connecting Rod Bearings Installation.Figure 10. Oil Distribution Inlet Tube and Screen Hardware Installation.Install port thermostat housing (WP 0141).SUSTAINMENT MAINTENANCE PISTON AND CYLINDER LINER REBUILDSlide the piston (1) out through the bottom of the cylinder liner (2).Slide the piston pin (10) from the piston (1).Use compressed air to dry piston crown.3. Check the tapered fire ring groove width in the piston crown (12) with groove gage.Inspect the liners (2) for poor contact on the outer surfaces.Measure the inside bore of the cylinder liner at (A, B, C, D, E, F and G) on both the (X) and (Y) axis.{1} Calculate the general inside diameter of the liner, it should measure a minimum of 4.8390 in.{3} Clamp the liner into place with hold down clamp.Hold the piston assembly (1) in one hand by the piston skirt (11).Using the skirt of the piston (1), push the ring down slightlyEnsure the piston ring grooves are clean and free of debris.1. Install new compression and fire rings (5).Lightly coat threads of bolt (8) with engine oil.10. Ensure the piston pin retainer (7) is seated properly.Lubricate the inside of the cylinder liner (2) with engine oil.VIBRATION DAMPENER REPLACEMENTFigure 1. Vibration Dampener Removal.Figure 2. Inner Cone Installation.Figure 4. Vibration Dampener/Hub Assembly.Figure 5. Vibration Dampener Installation.FRONT BALANCE WEIGHT COVER REPAIRDry cover (Figure 1, Item 1) with compressed air.Figure 1. Oil Seal Removal.Lightly lubricate outer surface of new oil seal with lubricating oil.Figure 2. Oil Seal Installation.FRONT BALANCE WEIGHT COVER REMOVAL AND INSTALLATIONFigure 1. Front Balance Weight Cover.Remove gasket (Figure 2, Item 2) and discard.Install engine forward lifting bracket (WP 0135).FUEL SYSTEM PRIMINGFigure 2. Fuel Priming Pump.FUEL FILTER CARTRIDGE REPLACEMENTFigure 1. A3 Breaker Switch.Figure 2. Fuel Filter Adapter Removal.Remove LO/TO from A3 breaker switch. Refer to FM 4-01.502 for LO/TO procedure.FUEL HOSES AND TUBES REPLACEMENTFigure 1. A3 Breaker Switch.Figure 2. Fuel Supply and Return Valves.REMOVAL FUEL RUBBER HOSESStart engine (TM 55-1925-205-10).FUEL COOLER REPLACEMENTFigure 2. Butterfly Valve.Figure 3. Fuel Cooler Removal.Figure 4. Fuel Cooler Removal.Figure 5. Fuel Cooler Installation.Figure 6. Fuel Cooler Hoses Installation.Clean up spilled fluids with spill clean-up kitFUEL COOLER MOUNTING BRACKET REPLACEMENTFigure 1. Fuel Cooler Bracket.FUEL FILTER ADAPTER REPAIRPlace a drain pan under fuel filter adapter (Figure 1, Item 8).Figure 1. Fuel Filter Adapter Removal.Figure 2. Fuel Filter Adapter Removal and Installation.Figure 3. Fuel Filter Adapter Installation.FUEL FILTER MOUNTING BRACKET REPLACEMENTPerform operational check of diesel engine (TM 55-1925-205-10).FUEL ADAPTER BLOCK REPLACEMENTFigure 1. Fuel Adapter Block Lines Removal.Figure 2. Fuel Adapter Block Removal.Figure 3. Fuel Adapter Block Installation.Figure 4. Fuel Adapter Block Lines Installation.FUEL INJECTOR CONTROL TUBE AND LEVER ASSEMBLY REMOVAL AND INSTALLATIONDisengage rack control levers from injector control racks.Figure 1. Fuel Injector Control Tube.FUEL INJECTOR CONTROL TUBE AND LEVER ASSEMBLY REPAIRRemove stationary bracket from control tube.Figure 1. Injector Rack.Remove control lever from injector control tube assembly.Figure 2. Indexing Bracket and Injector Control Tube.Figure 3. Injector Control Tube.FUEL INJECTOR MODULATOR ASSEMBLY REMOVAL AND INSTALLATIONFigure 1. Fuel Modulator Removal and Installation.Figure 2. Control Tube.FUEL IGNITION MODULATOR ASSEMBLY REPAIRUsing cleaner, clean modulator assembly components.Install pin and roller on lever assembly.FUEL IGNITION MODULATOR ASSEMBLY ADJUSTMENTFigure 2. Injector Body.Figure 3. Ignition Modulator Adjustment.Install cylinder head poppet valve rocker arm cover (WP 0044).FUEL INJECTOR ASSEMBLY REMOVAL, CLEANING, INSPECTION AND INSTALLATIONSlide injector control rack lever (3) away from injector control rack (4).Cover injector hole (9) with clean, lint free cloth.Inspect injector follower spring for rust and corrosion. If found, replace fuel injector.6. Slide injector rack control lever (3) into injector control rack (4).19. Install intake plenum assembly. (TM 55-1945-205-24-3-1)FUEL INJECTOR TIMING ADJUSTMENTFigure 2. Exhaust Valves.Figure 3. Injector Adjustment.FUEL INJECTOR RACK CONTROL LEVER ADJUSTMENTFigure 1. Fuel Supply and Return Valves.Figure 3. Right Cylinder Head.Figure 5. Left Cylinder Head.Verify the adjustment of the control lever is not too tight.Disconnect the fuel rod from the clevis leverTighten the adjusting screw an additional 1/8 turn.Figure 8. Left Cylinder Head.Figure 10. Left Cylinder Head.Repeat Steps 33 through 36 for remaining two injector rack control leversFigure 11. S1 SwitchFUEL PUMP REMOVAL AND INSTALLATIONFigure 1. A3 Breaker Switch.Figure 2. Fuel Valves.Figure 3. Fuel Pump.Install heat exchanger (WP 0134).FUEL PUMP REPAIRFigure 2. Fuel Pump Secured in Vise.Figure 4. Driveshaft, Drive Gear and Retaining Ball Disassembly.Figure 5. Relief Valve Plug Disassembly.Figure 6. Oil Seal Removal.Inspect driven shaft for wear or scoring. Replace defective parts.Figure 7. Fuel Pump On Wooden Wedges.Ensure fuel pump body sits flush on wedge woodFigure 10. Relief Valve Plug Assembly.Figure 11. Driveshaft, Drive Gear and Retaining Ball Assembly.Use lubricating oil to lubricate gear assembly (Figure 13, Item 7).Figure 14. Fuel Pump Elbow Fitting Installation.FUEL PRIMING PUMP REPLACEMENTFigure 2. Fuel Supply and Return Valves.Figure 3. Fuel Priming Pump.Clean up spilled fluid with a spill clean-up kit and disposeELECTRONIC GOVERNOR ROD ASSEMBLY REPAIRFigure 1. A3 Breaker Switch.Figure 2. Electronic Governor.ELECTRONIC GOVERNOR ACTUATOR REPLACEMENTFigure 1. A3 Breaker Switch.Figure 2. Electronic Governor Actuator.Figure 3. Governor Actuator.ELECTRONIC GOVERNOR CONTROLLER REPLACEMENTRemove governor controller (Figure 2, Item 2).Figure 2. Electrical Enclosure.Start the engine TM 55-1925-205-10.Figure 3. Electronic Governor Controller.Figure 4. Actuator Lever.Figure 5. Electrical Enclosure.ELECTRONIC GOVERNOR MAGNETIC PICK-UP REPLACEMENTFlywheel & Electronic Governor.Install electronic control valve (TM 55-1925-319-23).ELECTRONIC GOVERNOR DRIVE ASSEMBLY REMOVAL AND INSTALLATIONFigure 1. Injector Rack and Fuel Rods.Figure 2. Governor Drive.Install intake plenum assembly (TM 55-1925-205-10).ELECTRONIC GOVERNOR DRIVE ASSEMBLY REPAIRFigure 1. Electronic Governor Drive Assembly.Clean all parts with cleaner.Install woodruff key into shaft of shaft and lever assembly.AIR INTAKE HOUSING REPAIRFigure 1. A3 Breaker Switch.Figure 3. Blower Gasket Removal.Using type II cleaner, clean all parts of dirt and grease.Figure 4. Springs and Valves.Figure 5. Blower Gasket Installation.Figure 6. Air Intake Housing Installation.AIR INLET COLLECTOR ASSEMBLY REPLACEMENTSlide collector assembly out of band.Figure 1. Collector Assembly.AIR INLET COLLECTOR ASSEMBLY REPAIRCoat air filter element with filter element oil from filter cleaning kitUse cleaner to clean retainer springs, air inlet collector assemblyFigure 2. Air Inlet Collector Disassembly.CRANKCASE BREATHER LIMITER ASSEMBLY REPLACEMENTRemove six hose clamps (Figure 1, Item 1) from hoses (Figure 1, Item 2).CRANKCASE VENTILATION BREATHER PIPE REPLACEMENTFigure 1. Crankcase Breather Hose.Figure 2. Crankcase Breather Hose Elbow.Install electronic governor actuator (WP 0098).BLOWER BYPASS VALVE REPLACEMENTRemove hose (Figure 2, Item 2) from valve (Figure 2, Item 7).Perform operational check of diesel engineBLOWER DRIVESHAFT AND SPRING ASSEMBLY REPLACEMENTFigure 1. Broken Blower Driveshaft Portion Removal.Figure 3. Blower Driveshaft Retaining Ring.Install driveshaft alignment tool into hole of blower driveshaftInstall electronic governor actuator (WP 0098).BLOWER REMOVAL AND INSTALLATIONUsing sling, lift blower (Figure 1, Item 2) up and away from blockFigure 1. Blower.Using torque wrench and socket set, tighten four long boltsPerform operational check of diesel engine (TM 55-1925-205-10).BLOWER ASSEMBLY REPAIRRemove nine bolts (Figure 1, Item 2) and washersBoth gears must be pulled at the same time.Remove two fillister head screws securing rear end plateRemove fuel pump drive bolt (Figure 5, Item 5), lock washersRemove bearings (Figure 7, Item 4), oil sealsRemove seal rings and seal ring carriers and bearing race from rotor shaftsDiscard oil seal ring carriers (Figure 9, Item 6)Examine the blower timing gearsInstall the oversize seal and sleeve.Install remaining oversize seal sleeves on rotorsInstall the blower front end plate.Install blower rotors in the blower housing.Install the blower rear end plate (Figure 15, Item 4).h. Using a torque wrench and screwdriver socket wrench set, torqueInstall rear blower rotor shaft bearingsReverse the position of the blower housingInstall self locking screws.Lubricate the splines with light engine oil.Figure 20. VIEWS FROM GEAR END OF BLOWER.Check the clearance between each rotor lobeTable 1. Chart of Minimum Blower Clearances.Table 1. Chart of Minimum Blower Clearances - Continued.BLOWER DRIVE ASSEMBLY REMOVAL AND INSTALLATIONFigure 1. Blower Hardware.Figure 2. Blower Drive.BLOWER DRIVE ASSEMBLY REPAIRFigure 2. Spring Plates.Figure 4. Thrust Washers.Clean all metal parts with cleaner.Place blower support shaft into soft jaw vise caps of vise.TURBOCHARGER REPLACEMENTFigure 1. Turbo Exhaust Elbow Removal.Figure 2. Turbocharger Removal.Figure 4. Oil Drain Hose Removal.Figure 5. Exhaust Flange Removal.Figure 6. Turbocharger Gasket Installation.Figure 8. Coolant Lines Installation.Figure 9. Turbocharger Exhaust Elbow Installation.Install air intake housing (WP 0103).LUBE OIL SYSTEM CRANKCASE SERVICINGFigure 1. A3 Breaker Switch.Connect a combination hose coupling and pipe nipple to end of pump suction hose.Figure 2. Dust Cap.Figure 3. Dipstick.Replace dust cap on forward coupling half.LUBE OIL SYSTEM CRANKCASE PRESSURE TESTINGFigure 2. Oil Level Dipstick.Shut down engine (TM 55-1925-205-10).LUBE OIL SYSTEM TURBOCHARGER FLANGED OIL TUBE TO ENGINE OIL HOSE REPLACEMENTPosition drain pan under flanged oil tubeFigure 2. Flanged Oil Tubes.LUBE OIL SYSTEM HOSES REPLACEMENTUsing a wrench, hold the elbow or fittingFigure 1. Oil Hoses Replacement.LUBE OIL PUMP REMOVAL AND INSTALLATIONFigure 1. Oil Pump Brackets.Figure 2. Oil Pump.Using oil seal expander with guide studs, install oil pumpInstall air box covers (WP 0036).LUBE OIL PUMP REPAIRFigure 1. Oil Pump Gear Retaining Plate.Clean all metal parts with cleaner.Figure 2. Oil Pump Gears.Figure 3. Front Cover Assembly.LUBE OIL PUMP INLET SCREEN REMOVAL, CLEANING, INSPECTION, AND INSTALLATIONRemove screen (Figure 1, Item 5) from cover (Figure 1, Item 1).Figure 1. Oil Pump Inlet Screen.Install exhaust manifolds (WP 0157).LUBE OIL SYSTEM DISTRIBUTION COMPONENTS REMOVAL, CLEANING, INSPECTION, AND INSTALLATIONFigure 1. Lube Oil System Distribution Components.Remove two support brackets as follows:Using torque wrench, torque boltsto 156 to 204 in-lbLUBE OIL PRESSURE REGULATOR VALVE REMOVAL AND INSTALLATIONFigure 1. Lube Oil Pressure Regulator Valve.Remove engine from stand (WP 0033).LUBE OIL PRESSURE REGULATOR VALVE REPAIRRemove lube oil pressure regulator valve bodyInspect spring for deformation, pitting, breaks or corrosion. Replace defective part.LUBE OIL PRESSURE RELIEF VALVE REMOVAL AND INSTALLATIONFigure 1. Lube Oil Pressure Relief Valve Removal and Installation.Remove engine from stand (WP 0033).LUBE OIL PRESSURE RELIEF VALVE REPAIRFigure 1. Vise With Lube Oil Pressure Relief Valve Body.Remove lube oil pressure relief valve bodyInsert lube oil pressure relief valveLUBE OIL PAN REPLACEMENTFigure 1. Oil Pan.Using cleaner, clean new oil pan (Figure 2, Item 2).Figure 2. Oil Pan Gasket.Install marine gear oil cooler (TM 55-2040-211-24).LUBE OIL COOLER REPLACEMENTFigure 1. A3 Breaker Switch.Figure 2. Oil Filter Supply Lines.Figure 4. Cover Plate Removal.Figure 6. Cover Plates Removal.Figure 8. Oil Cooler Mounting Plates Removal.Use cleaner and a force pump to clean oil cooler core oil passages, as follows:Remove drain pan and dispose of contents in accordance with local procedures.Figure 9. Oil Cooler Mounting Plates Installation.Figure 11. Oil Cooler Installation.Figure 13. Mounting Hardware Installation.Figure 15. Oil Cooler Housing Installation.Perform operational checks (TM 55-1925-205-10).LUBE OIL COOLER BYPASS VALVE REPLACEMENTFigure 1. Oil Cooler Adapter.Figure 2. Oil Cooler Adapter.LUBE OIL DIPSTICK TUBE ASSEMBLY REPLACEMENTRemove O-ring from lube oil dipstick tube assemblyPerform operational checks (TM 55-1925-205-10).LUBE OIL PRESSURE SENDING UNIT REPLACEMENTTag and disconnect two wires from oil pressure sending unitClean spilled fluid with spill clean-up kitLUBE OIL TEMPERATURE SWITCH REPLACEMENTPosition a drain pan under lube oil temperature switchPerform operational check of the diesel engine (TM 55-1925-205-10).FRESH WATER COOLING SYSTEM FLUSHPlace A3 breaker switch, located on A10 panelPosition drain pan under drain cocksRemove engine thermostats and install thermostat coversFigure 2. Coolant Drain Cocks.Remove drain pans and dispose of contentsFigure 3. Coolant Flush Drain Cocks.Drain cooling system completely, as follows:Figure 4. Coolant Drain Cocks.Ensure drain cocks are closed.Figure 5. Pressure Control Cap.Perform operational checks (TM 55-1925-205-10).FRESH WATER COOLING SYSTEM HEAT EXCHANGER REPLACEMENTLoosen clamp on inlet hose/tube assemblyFigure 2. Expansion Tank Removal.Install new gasket on new heat exchanger coreFigure 3. Expansion Tank Installation.FORWARD LIFTING BRACKET REPLACEMENTRemove support (Figure 1, Item 1) from engineInstall heat exchanger (WP 0134).FRESH WATER COOLING SYSTEM FILTER ELEMENT REPLACEMENTFigure 2. Fresh Water Filter Valves.FRESH WATER COOLING SYSTEM FILTER HEAD COVER REPLACEMENTPlace drain pan under filter coverFigure 2. Filter Head Cover.Wrap bushing threads with antiseizing tape.Install fresh water cooling system filter (WP 0136).FRESH WATER COOLING SYSTEM FILTER HEAD COVER MOUNTING BRACKET REPLACEMENTFigure 2. Heat Exchanger.Figure 3. Mounting Bracket.Install fresh water cooling system filter (WP 0137).FRESH WATER COOLING SYSTEM THERMOSTAT REPLACEMENTRemove port thermostats (Figure 1, Item 5).Figure 1. Port Thermostats.Figure 2. Starboard Thermostats.Figure 3. Port Thermostats.Figure 4. Starboard Thermostats.Install fresh water cooling system bypass tube (WP 0143).FRESH WATER COOLING SYSTEM STARBOARD THERMOSTAT HOUSING REPLACEMENTApply sealing compound to gasket surface of cylinder headInstall fresh water cooling system thermostat (WP 0139).FRESH WATER COOLING SYSTEM PORT THERMOSTAT HOUSING REPLACEMENTUsing putty knife, clean gasket surface of cylinder headFigure 1. Thermostat Housing.Shut engine down (TM 55-1925-205-10).FRESH WATER TEMPERATURE SENDING UNIT REPLACEMENTRemove drain pan and dispose of contents in accordance with local procedures.Figure 2. Thermostat Housing.FRESH WATER COOLING SYSTEM BYPASS HOSES REPLACEMENTFigure 1. Cooling System Bypass Hoses.Service fresh water cooling system (TM 55-1925-205-10).FRESH WATER COOLING SYSTEM COOLANT HOSES REPLACEMENTFigure 1. Cooling Hose.Drain residual coolant into drain pan.Fill cooling system (TM 55-1925-205-10).FRESH WATER COOLING SYSTEM PORT WATER OUTLET MANIFOLD REPLACEMENTFigure 1. Fresh Water Cooling System Port Water Outlet Manifold.Install new gaskets (Figure 1, Item 10) on cylinder headFRESH WATER COOLING SYSTEM STARBOARD WATER OUTLET MANIFOLD REPLACEMENTFigure 1. Fresh Water Cooling System Starboard Water Outlet Manifold.Position new water outlet manifoldFRESH WATER COOLING SYSTEM PUMP REPLACEMENTFigure 1. Pump Body.Figure 3. Water Pump Body.Figure 4. Water Pump Cover.Install fuel system fuel filter (WP 0079).FRESH WATER COOLING SYSTEM PUMP DRIVE GEAR REPLACEMENTInstall new woodruff key on shaftInstall camshaft vibration damper (WP 0064).FRESH WATER COOLING SYSTEM PUMP REPAIRUsing retaining ring pliers, slide pliers into slot of gearInstall impeller puller onto impellerUsing a brass drift as a buffer between the arbor press14. Remove inner bearingLubricate the bearing surface of the new shaft with grease.10. Install the new oil seal in the pump bodyInstall gear installation tool on threaded end of shaft.Apply a thin coat of adhesive to outside diameter of water sealAFTERCOOLER REPLACEMENTVerify fuel supply and return valvesFigure 3. Engine Aftercooler.Tighten hose clamps (Figure 3, Item 9).FUEL COOLER ZINC ANODE PLUG REPLACEMENTRemove zinc anode from fuel coolerTighten zinc anode (Figure 3, Item 2).MARINE GEAR COOLER ZINC ANODE PLUG REPLACEMENTVerify butterfly valve on seachest is off.Figure 3. Zinc Anode.HEAT EXCHANGER ZINC ANODE PLUG REPLACEMENTFigure 2. Butterfly Valve.Wrap support plug threads with antiseizing tape.RAW WATER PUMP ZINC ANODE PLUG REPLACEMENTFigure 2. Butterfly Valve.Figure 3. Raw Water Pump.RAW WATER PUMP REPLACEMENTFigure 2. Raw Water Pump and Tubes.Figure 3. Outlet Elbow.Figure 4. Raw Water Pump.Figure 5. Outlet Elbow.Start engine and verify there are no leaksRAW WATER PUMP REPAIRFigure 1. Raw Water Pump.Figure 3. Drive Gear.Figure 4. Arbor Press.Figure 5. Slinger and Bearing Seal.Figure 7. Slotted Screw, Cam, and Wear Plate.Support bearing on wooden wedges.EXHAUST MANIFOLD REPLACEMENTFigure 1. Water Inlet Tube.Using torque wrench and socket set, torque boltsInstall six bolts (Figure 1, Item 5) and new lockwashersMARINE GEAR OIL COOLER MOUNTING BRACKET REPLACEMENTFigure 1. Mounting Bracket.ELECTRICAL SYSTEM NORMAL STOP PUSHBUTTON REPLACEMENTRemove cover (Figure 2, Item 4) from boxPerform operational check of diesel engineELECTRICAL SYSTEM NORMAL STOP PUSHBUTTON MOUNTING BRACKET REPLACEMENTFigure 1. Mounting Bracket.ELECTRICAL SYSTEM HOUR METER REPLACEMENTFigure 2. Hour Meter Bracket.ELECTRICAL SYSTEM HOUR METER MOUNTING BRACKET REPLACEMENTFigure 2. Hour Meter Mounting Bracket.STARTER RELAY REPLACEMENTRemove two bolts, lockwashers, and nutsFigure 2. Starter Relay.STARTING MOTOR REPLACEMENTTag and remove wires from solenoid switchFigure 1. Starter Motor.ENGINE COLD PACK STARTING AID REPLACEMENTRemove cylinder by turning it counterclockwise.Figure 1. Cold Pack Starting Aid.COLD START TEMPERATURE SWITCH REPLACEMENTFigure 2. Cold Start Switch.TACHOMETER SENDING UNIT REPLACEMENTFigure 2. Tachometer Sending Unit.TACHOMETER DRIVE REPAIRInstall new tachometer drive in housing assemblyInstall tachometer sending unit (WP 0167).OVERSPEED GOVERNOR REPLACEMENT AND ADJUSTMENTFigure 2. Overspeed Governor Box Cover Removal.Figure 3. Stuffing Tube.Figure 4. Mounting Plate and Speed Switch.Figure 5. Set Points.Verify ohmmeter reads zero ohms.Figure 6. Jumper Terminals.Figure 7. Overspeed Governor Box Cover Installation.AUTO SHUTDOWN SYSTEM EMERGENCY STOP SOLENOID REPLACEMENTTag emergency stop solenoid electrical wireFigure 3. Emergency Stop Solenoid Link.Figure 5. Emergency Stop Solenoid Bracket.Figure 7. Emergency Stop Solenoid Mounting.Figure 8. Emergency Stop Solenoid Link.Install SINCGARS antenna (TM 11-5820-890-10-8).AUTO SHUTDOWN SYSTEM HIGH WATER TEMPERATURE SWITCH REPLACEMENTTag and disconnect wires from switchService fresh water cooling system (TM 55-1925-205-23).AUTO SHUTDOWN SYSTEM LOW OIL PRESSURE SWITCH REPLACEMENTTag and disconnect wires from oil pressure switchFigure 2. Oil Pressure Switch.AUTO SHUTDOWN SYSTEM FUEL OIL PRESSURE SWITCH REPLACEMENTFigure 2. Fuel Supply and Return Valves.Figure 3. Fuel Oil Pressure Switch.Perform operational check of diesel engineTORQUE LIMITSFigure 2. Torque Wrench Adapter Centerline.Figure 4. Bolt Head Markings.Table 1. SAE Standard Torque Table.Table 2. SAE Standard Torque Table.Table 3. Metric Standard Torque Table.Table 4. Metric Standard Torque Table.CHAPTER 4 - SUPPORTING INFORMATIONREFERENCESSUPPLY CATALOGSMAINTENANCE ALLOCATION CHART (MAC) INTRODUCTIONMaintenance FunctionsExplanation of Columns in the MACExplanation of Columns in the Tools and Test Equipment RequirementsTable 1. Maintenance Allocation Chart for EngineTable 1. MAC for Engine - Continued.Table 1. MAC for Engine - Continued.Table 1. MAC for Engine - Continued.Table 1. MAC for Engine - Continued.Table 1. MAC for Engine - Continued.Table 1. MAC for Engine - Continued.Table 1. MAC for Engine - Continued.Table 1. MAC for Engine - Continued.Table 1. MAC for Engine - Continued.Table 2. Tools and Test Equipment Requirements for EngineTable 2. Tools and Test Equipment Requirements for Engine - Continued.Table 2. Tools and Test Equipment Requirements for Engine - Continued.Table 2. Tools and Test Equipment Requirements for Engine - Continued.Table 2. Tools and Test Equipment Requirements for Engine - Continued.Table 2. Tools and Test Equipment Requirements for Engine - Continued.Table 2. Tools and Test Equipment Requirements for Engine - Continued.EXPENDABLE AND DURABLE ITEMS LIST (EDIL)Table 1. Expendable and Durable Items ListTable 1. Expendable and Durable Items List - Continued.Table 1. Expendable and Durable Items List - Continued.WARPING TUG DIESEL ENGINE TOOL IDENTIFICATION LIST (TIL)Table 1. Tool Identification List. (TIL) (Continued)Table 1. Tool Identification List. (TIL) (Continued)Table 1. Tool Identification List. (TIL) (Continued)Table 1. Tool Identification List. (TIL) (Continued)Table 1. Tool Identification List. (TIL) (Continued)Table 1. Tool Identification List. (TIL) (Continued)MANDATORY REPLACEMENT PARTS (MRP) LISTTable 1. Mandatory Replacement Parts ListTable 1. Mandatory Replacement Parts List - Continued.Table 1. Mandatory Replacement Parts List - Continued.Table 1. Mandatory Replacement Parts List - Continued.Table 1. Mandatory Replacement Parts List - Continued.Table 1. Mandatory Replacement Parts List - Continued.Table 1. Mandatory Replacement Parts List - Continued.Table 1. Mandatory Replacement Parts List - Continued.
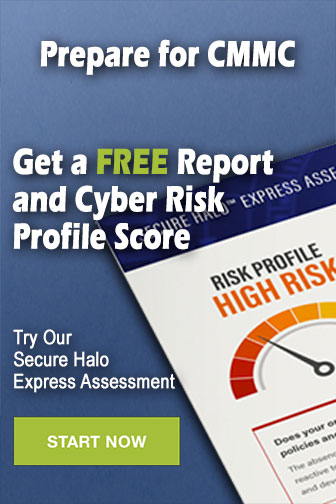