LEARNING OBJECTIVESSAFETY RESPONSIBILITIESENFORCING SAFETYTAGS, LABELS, AND MARKINGSSAFETY EQUIPMENTMACHINE/EQUIPMENT SAFETYCHEMICAL/SOLVENT HAZARDSWELDING HAZARDS AND PRECAUTIONSSOLDERING AND BRAZING SAFETY PRACTICESRESUSCITATIONCardiopulmonary ResuscitationUse of a TourniquetPressure points for control of bleeding.First-, second-, and third-degree burns.Rule of Nines.HEARING CONSERVATION AND NOISE ABATEMENTMONITORING HEARING TESTSSUMMARYSHIP REPAIRALTERATIONS EQUIVALENT TO REPAIRSAMALGAMATED MILITARY AND TECHNICAL IMPROVEMENT PLANREPAIR ACTIVITIESIMA AvailabilitiesDIVING AND SALVAGE OFFICERAutomated Work Request.MACHINERY REPAIR DIVISION (R-2).CONCEPTS OF QUALITY ASSURANCETHE QA LINK TO MAINTENANCEShip Quality Control InspectorREPAIR PROCEDURESPLANNING AND SCHEDULING JOBSChecking on MaterialsEstimating time required for a gangway repair job.WEIGHT CONSIDERATIONSPriority of WorkAssigning WorkHandling Materials and EquipmentSTOWAGE REQUIREMENTSTypes of frames used on board ship.Basic frame section (longitudinal framing).STERN STRUCTUREBulbous-bow configuration.Stern Structure.STANCHIONSSUMMARYWOODWORKING CUTS AND JOINTSTREE GROWTH AND STRUCTURECUTTING LUMBERLUMBER DEFECTS AND BLEMISHESLUMBER SIZESMEASURING LUMBERCOMMON TYPES OF WOODSCommon Woods--ContinuedCommon Woods--ContinuedCommon Woods--ContinuedKinds of LumberCare and Storage of LumberTypical Douglas fir back stamp.STANDARD JOINTSDovetail JointsMortise-and-Tenon JointsFigure 3-18.--Box corner joint.Half-Lap JointsFigure 3-22.--Planing and squaring to dimension.Figure 3-24.--Gross half-lap joint.Grooved JointsFigure 3-25.--Dado and rabbet joint.Figure 3-27.--Dovetail half-lap joint.Box Corner and Miter JointsMortise-and-Tenon JointsFigure 3-34.--Kerf jig for mitered joints.Figure 3-35.--Slip feather reinforcement.Figure 3-37.--Mortise-and-tenon joints. A. Stub. B. Haunched. C. Table-haunched.Figure 3-41.--Panel construction.FASTENING MATERIALSMethods of Applying GlueNAILS, BRADS, DOWELS, AND CORRUGATED FASTENERSFigure 3-49.--Types of nails and nail sizes.Wood ScrewsFigure 3-51.--Types of wood screws and nomenclature.Table 3-3.--Screw Sizes and DimensionsSANDING MATERIALSTable 3-6.--Abrasive RecommendationsLATHE SANDINGFigure 3-55.--Sanding a lathe job.BOAT REPAIR AND DECK COVERINGSFigure 4-1.--A 26-foot Mk 10 motor whaleboat.Figure 4-4.--A 36-foot Mk 11 LCPL.EMERGENCY REPAIRSFERROCEMENT BOATSPLASTIC BOATSBasic ConsiderationsFigure 4-7.--Types of patches applied to reinforced plastic boats.PLANNING THE REPAIRFigure 4-9.--Estimating materials.PREPARING THE DAMAGED AREAFigure 4-12.--Scarfing operation.Figure 4-13.--Placing shoring over a film-covered backing plate.Figure 4-14.--Entire patch being put in place.Figure 4-15.--Heat lamps in position to speed the cure.Bolthole RepairFigure 4-17.--Typical stiffeners.Figure 4-l8.--Cutting the patch from preformed laminate.Figure 4-21.--Coating the scarfed side of a damaged boat.METAL BOATSALUMINUM BOAT REPAIRSTEEL BOAT REPAIRFigure 4-25.--Boat chock for shipboard use.Figure 4-27.--Using the template.REPAIRING THE SHEER CLAMPFigure 4-31.--Transom construction.Figure 4-34.--Deck supports and transom knee.RUBBER TILE OR ROLL DECKING MATERIALSApplication of Deck TileRUBBER TERRAZZO]NONSKID DECK TREADSTOOLS AND EQUIPMENTFigure 5-1.--Torque wrenches.CALIPERSCaliper MaintenanceFigure 5-4.--Thickness (feeler) gauges.Figure 5-7.--Steel plate and sheet metal gauges and thicknesses.Combination SquareFigure 5-9.--Steel square.Figure 5-11.--Combination square.WOOD- AND METAL-BORING BITSFigure 5-16.--Size markings on auger bits.Table 5-1.--Twist Drill SizesMACHINE SPUR BITMETAL-CUTTING TOOLSFigure 5-24.--File information.Care of FilesUsing HacksawsELECTRICAL POWER TOOLSPNEUMATIC POWER TOOLSFigure 5-35.--Pneumatic rivet setting tools.THREAD-CUTTING TOOLSTAPS AND DIESFigure 5-37.--Types of solid dies.Figure 5-39.--Diestocks, diecollet, and tap wrenches.THREAD CHASERSFigure 5-46.--Oversize drilled hole for tapping.Table 5-2.--American National Form ThreadsCutting Machine Threads With TapsINSTALLED MACHINE TOOLSFigure 5-53.--Power hacksaw.Hacksaw BladesFigure 5-55.--Tiltable blade metal-cutting bandsaw.GRINDERSGrinding SafetyWHEEL MARKINGS AND COMPOSITIONFigure 5-61.-- How bond affects the grade of a wheel. WheelRINDING WHEEL SELECTION AND USEWHEEL INSTALLATIONTRUING AND DRESSING THE WHEELGAS CYLINDERS AND CYLINDER VALVESCONSTRUCTION OF CYLINDERSColor Codes for CylindersTable 5-4.--Cylinder Color CodeTESTING AND REPAIRING CYLINDERSHandling CylindersReady-Service Storage RulesGAS CYLINDER VALVESSafety Devices for ValvesSUMMARYMETALLURGYIRON AND STEELTENSION STRESSBENDING STRESSFigure 6-6.--Grain structure in metals.INTERMETALLIC COMPOUNDS PROPERTIES OF METALMETAL FATIGUEPLASTICITYDUCTILITY AND MALLEABILITYTYPES OF METALAlloy SteelAluminum and Aluminum AlloysIDENTIFICATION TESTSFigure 6-10.--Fundamental spark forms.Figure 6-11.--spark pictures formed by common metals.Oxyacetylene Torch TestFracture TestTable 6-5.--Identification of Metals by Chip TestNitric Acid TestSUMMARYINTRODUCTION TO WELDING AND CUTTINGFigure 7-1.--Welding processes.INTIMACY OF CONTACTWELDABILITYTYPES OF JOINTSFigure 7-3.--Bead and fillet welds.Figure 7-4.--Standard groove welds.PARTS OF WELDSFigure 7-9.--Legs and throat of fillet weld.Figure 7-11.--Groove face, root face, and root edge.WELDING POSITIONSFigure 7-15.--Positions for welding pipe.Figure 7-16.--(A) Backstep sequence; (B) Wandering seqeunceFigure 7-17.--Multiple-pass layers.WELD DEFECTSFLUXESEXPANSION AND CONTRACTIONWELDING PIPINGP-1 CLASS PIPINGP-LT CLASS PIPINGSAFETY PRECAUTIONSLOCATION OF WELDINGOPERATION OF EQUIPMENTOPERATION OF EQUIPMENT - ContinuedSAFETY OF PERSONNELTable 7-1.--Eye Protection Shade GuidelinesSOURCES OF INFORMATIONOXYACETYLENE CUTTING AND WELDINGFigure 8-1.--A portable oxyacetylene outfit.MAPP Gas SafetyWELDING TORCHESFigure 8-7.--Equal-pressure welding torch.WELDING RODSADJUSTING THE FLAMEFigure 8-8.--Characteristics of the oxyacetylene flame.OXYACETYLENE CUTTINGFigure 8-10.--Cutting attachment for an oxyacetylene cutting torch.Figure 8-11.--Common cutting torch tips and their uses.Figure 8-12.--Cutting tips in various conditions.MAPP Gas Cutting TipsOXYACETYLENE CUTTING OPERATIONSBeveling PlateFigure 8-18.--Fabricating a T fitting.Cutting RivetsFigure 8-21.--Cutting a countersunk rivet with a low-velocity cutting tip.Special Cutting TechniquesJudging the Quality of Oxyacetylene CutsSAFETY PRECAUTIONSFigure 8-26.--Forehand welding.PRACTICE PROJECTSMaking a Butt Joint (Flat Position)Making a Corner JointFigure 8-36.--Edge preparation required for various types of T joints.GUIDE FOR OXYACETYLENE WELDING OF NONFERROUS METALSNickel and High-Nickel AlloysSAFETY PRECAUTIONSSUMMARYBRAZING AND BRAZE WELDINGSILVER BRAZING FILLER METALSTable 9-1.--Tip Sizes and Gas Pressures for Silver Brazing Various Thicknesses of MetalTable 9-2.--Silver Brazing Metals Commonly Used in the NavyTYPES OF JOINTSSILVER BRAZING TECHNIQUESFigure 9-6.--Flow of flux and filler metal.Figure 9-8.--Applying heat for silver brazing a tube and fitting.Figure 9-9.--Insert method of silver brazing.Figure 9-10.--Feed-in method of silver brazing.Table 9-5.--Class P-3a Special Brazed Joint CategoriesSILVER BRAZING TECHNIQUES - ContinuedBRAZE WELDINGBRAZE WELDING - ContinuedSURFACINGFigure 9-13.--Surfacing a lathe cutting tool.POWDERED METAL FLAME PROCESSFigure 9-14.--Powdered metal torch and accessories.Table 9-6.--Powdered Metal Alloys and Some of Their UsesOPERATING PROCEDURESFigure 9-18.--Making a powdered metal overlay deposit.PRECAUTIONSSOLDERINGTable 9-7.--Selection of Soldering Iron for Work to be Done by Copper Bit SizeCleaning Soldering BitsTable 9-8.--Tin-lead Melting PointsSOLDERING WITH IRONSFigure 9-30.--Making solder beads.SOLDERING BY SWEATINGMETAL-ARC WELDING AND CUTTINGWELDING MACHINESFigure 10-2.--Reverse polarity and straight polarity.Figure 10-3.--Paralleling connection for a single-operator welding generator.Rectifier-Type Welding MachineGROUNDING ELECTRICAL WELDING EQUIPMENTELECTRODE HOLDERSCLASSIFICATION OF ELECTRODESTable 10-1.--Electrode ClassificationsPREPARATIONS FOR WELDINGTable 10-3.--Typical Current Ranges in Amperes for ElectrodesFigure 10-8.--Striking or brushing method of starting the arc.ARC-WELDING TECHNIQUESFigure 10-12.--Use of backing strips in welding butt joints.ARC BLOWDISTORTIONFigure 10-18.--Welding in the vertical position.Figure 10-19.--Dimensional changes due to restrained expansion and unrestrained contraction.Figure 10-20.--Electric induction coils set up for preheating pipeBASIC THEORY OF ALUMINUM WELDINGTable 10-4.--Causes and Cures of Common Welding ProblemsGeneral ConsiderationsTable 10-5.--Preheat Temperatures for Welding Sheet, Plate, and Tubular Aluminum Sections (Butt Joints)Figure 10-22.--Recommended joint designs for common thickness of plate.Welding Power SourceTable 10-6.--Current Selection for GTA WeldingWelding Equipment and SuppliesDual Action of the AC ArcFiller MetalSetting Up EquipmentEstablishing an Arc and Forming a Weld PoolFigure 10-31.--Forming a molten puddle with a GTA torch.Figure 10-33.--Comparative GTA weld beads as determined by electrical current.Flat-Position Single-Pass Butt WeldsHorizontal-Position Multipass Fillet and Butt WeldsVertical-Position Multipass Fillet and Butt WeldsHorizontal Fixed-Position Multipass WeldingGMA Welding EquipmentFigure 10-48.--CMA welding aluminum truck bed.Table 10-9.--Recommended Practices for GMA Welding of Aluminum AlloysFiller MetalFigure 10-52.--GMA welding. (A) Striking the arc. (B) Gun angle.Figure 10-53.--Reciprocating technique for GMA welding.Figure 10-56.--Acceptable single-pass and multipass GMA weldsFlat-Position Multipass Butt WeldsFigure 10-62.--Grass porosity in a multipass butt weld.Figure 10-66.--Welding a fillet and butt joint in the horizontal position.Vertical-Position Multipass Fillet and Butt WeldsFigure 10-70.--CMA gun manipulation for welding pipe in the horizontal fixed position.SAFETYSTUD WELDINGFigure 10-71.--Stud welding gun.ARC CUTTINGFigure 10-75.--Air carbon-arc gun.SUMMARYNONDESTRUCTIVE TESTS AND INSPECTIONS OF WELDSRADIOGRAPHYMaster ControlFigure 11-3.--Principle of X-ray generation.RADIOACTIVE SOURCERADIOGRAPHIC LIMITATIONSFigure 11-6.--Principles of shadow formation.CIRCULAR AND LONGITUDINAL MAGNETIZATIONFigure 11-7.--Circular magnetization--prod method.Defect RepairLIQUID PENETRANT INSPECTIONULTRASONIC TESTINGULTRASONIC PRINCIPLECalibration BlockFigure 11-13.--Scanning a weld.HYDROSTATIC TESTSHydrostatic Testing EquipmentHydrostatic Testing Equipment SetupPRESSURIZATIONOPERATIONAL TESTSSHEET METAL LAYOUT AND FABRICATIONFigure 12-3.--Drawing perpendicular parellel lines.Figure 12-6.--Setting the dividers.MAKING SIMPLE LAYOUTSFigure 12-14.--Variation of a cylinder.Figure 12-17.--Constructing a 90-degree angle by bisecting a line at a given point.Figure 12-19.--Bisecting an angle.Figure 12-22.--Layout of a square or rectangular elbow.Figure 12-24.--Double-hem edge.Figure 12-30.--Layout of Pittsburgh lock seam.LAYING OUT NOTCHESPARALLEL LINE METHODFigure 12-37.--Stretchout showing a girth line.Figure 12-38.--Elevation and plan of intersected pipe.Figure 12-41.--Pictorial view of pipe intersected at an angle.PARALLEL LINE METHOD - ContinuedFigure 12-46.--Stretchout of the T.RADIAL LINE METHODFigure 12-50.--Developement of a cone cut at any angle.TRIANGULATION METHODFigure 12-51.--Triangulation development of a twisted square.Figure 12-52.--Development of rectangular-to-round transition piece.Figure 12-53.--Development of offcenter round-to-round transition piece.TRANSFERRING THE PATTERNS TO METALFABRICATING SHEET METALFigure 12-59.--Power-driven squaring shears.Figure 12-62.--Ring-and-circle shear.Figure 12-63.--Cutting a disk with the ring-and-circle shear.Figure 12-67.--Cutting light sheet metal with a cold chisel.Figure 12-69.--Standard cornice brake.Figure 12-70.--Some steps in forming a Pittsburgh lock scam.Figure 12-72.--Box and pan brake (finger brake).Figure 12-75.--Slip-roll forming machine.Figure 12-76.--Forming a cylinder on a slip-roll forming machine.Figure 12-79.--Stakes and stake holder.Figure 12-81.--Hand forming a cone on a blowhorn stake.Specialized Metal Forming MachinesFigure 12-90.--Elbow edging rolls for combination rotary machineRIVETING SHEET METALFigure 12-95.--A hand punch.Figure 12-99.--Hand dolly used to back up rivets.Figure 12-102.--Pop rivet tools.Figure 12-103.--Fabricating a locker.MAINTENANCE AND REPAIR OF SHEET METAL STRUCTURESSTRUCTURAL STEEL FABRICATIONSTRUCTURAL STEEL STORAGEPARTS OF A BLUEPRINTLINES AND SYMBOLSFigure 13-4.--Bill of material.Figure 13-5.--Line standards.ADDITIONAL GUIDESFigure 13-7.--Orthographic projections.Figure 13-8.--Full- and half-sectional views.STRUCTURAL METAL SHAPESSTRUCTURAL STEEL SHAPESOTHER STEEL SHAPESSAE/AISI Classification SystemsFigure 13-17.--Steel plate and sheet metal gauges and thicknesses.Figure 13-19.--SAE classification.MILITARY SPECIFICATIONSNUMERICAL CLASSIFICATION SYSTEM.Material Cross-ReferencingCUTTING MACHINERYSHEAR NOMENCLATUREKNIFE SETTING AND CLEARANCE.Universal IronworkerFigure 13-23.--Universal ironworker.Figure 13-26.--Punch-to-die clearance.STOCK CUTTING OPERATIONSFigure 13-29.--Universal ironworker shear end.Figure 13-30.--Typical notcher and coper work.Figure 13-33.--Universal Pullmax machine.Figure 13-34.--Shearing tools.Plasma Arc MachinePlasma Arc TorchPLASMA ARC CUTTING PROCESSPress BrakeBRAKE PRESS SAFETYFigure 13-41.--Typical "V" die.Hossfeld BenderFigure 13-42.--Hossfeld Bender.Figure 13-43.--Standard parts and dies.Figure 13-44.--Types of templates and their use.BEND ALLOWANCEBend Allowance TermsComputing Bend AllowanceFigure 13-50.--Computing the overall length of a U-bolt.AVOIDING NOTCHES IN PLATEFigure 13-51.--Weld repair of partial and full penetration holes.Figure 13-52.--New inserts or patches crossing existing butt welds.Figure 13-53.--Access holes intersecting existing welds.Figure 13-54.--Patch removal involving more than two existing multiple cuts.STOPPING CRACKS IN PLATEFigure 13-55.--Ductile metal overlay to arrest cracks in surface ship hull structure.Figure 13-56.--Flame shrinkage used to correct distortion.Water Spray EquipmentFabricating a BracketFabricating a PadeyeFigure 13-65.--Fabricated bases, foundations, and supports.Figure 13-66.--Fabricated flat leaf hinge.SHOP MATHEMATICSDECIMAL FRACTIONConverting Fractions to DecimalsConverting Fractions to Decimals - ContinuedConverting Terminating Decimals to FractionsRATIO AND PROPORTIONGEOMETRIC CONSTRUCTIONBISECTING AN ARCFigure 14-7.--Drawing a circle through three given points.BLENDING ARCS AND TANGENTSDrawing Large Arcs Tangent to Smaller ArcsFigure 14-16.--Trial-and-error method of finding the center of a circle that passes through three given points.DRAWING PLANE FIGURESDRAWING A REGULAR HEXAGONDRAWING AN ELLIPSEConcentric-Circle MethodDRAWING SPIRALS AND INVOLUTESDrawing a Spiral of ArchimedesFigure 14-34.--Drawing a helix.Figure 14-37.--Areas and volumes for calculating weights of castings.Figure 14-37.--Areas and volumes for calculating weights of castings--Continued.PRINCIPLES OF SURFACE DEVELOPMENTFigure 14-37.--Areas and volumes for calculating weights of castings--Continued.Figure 14-37.--Areas and volumes for calculating weights of castings--Continued.Figure 14-38.--Three-dimensional shapes.PARALLEL DEVELOPMENTFigure 14-42.--Development of a truncated hexagonal prism.Figure 14-44.--Development for a four-piece elbow.Figure 14-46.--Development of a T-joint with two cylindrical pipes of unequal diameters.Figure 14-47.--Development of a round pipe joint made of two cylindrical pipes of unequal diameters, intersecting at an angle of other than 90.Figure 14-48.--Development of a pipe joint in which a rectangular pipe intersects a round pipe at an angle other than 90.Figure 14-50.--Development of a truncated pyramid.Figure 14-53.--Development of a truncated right cone.Figure 14-54.--Development by triangulation of a transition piece.Figure 14-55.--Development of a rectangular transition piece, which is not a true pyramid.Figure 14-56.--Development of a warped transition piece.Table 14-1.--Metric System and English ConversionTable 14-1.--Metric System and English Conversion--ContinuedTable 14-1.--Metric System and English Conversion--ContinuedTable 14-1.--Metric System and English Conversion--ContinuedTable 14-1.--Metric System and English Conversion--ContinuedTable 14-1.--Metric System and English Conversion--ContinuedTable 14-2.--Mathematics SymbolsTable 14-3.--Table of Decimal Equivalents of Fractions of an InchTable 14-4.--Weights and MeasuresTable 14-4.--Weights and Measures--ContinuedTable 14-5.--Rectangular CapacitiesTable 14-6.--Circular CapacitiesSUMMARYPIPING SYSTEMSTable 15-1.--Schedule Designations of Pipe SizeMETHODS OF MANUFACTURECHOICE OF MATERIAL AND SIZESFITTINGSFigure 15-3.--Typical pipe fittings.Figure 15-4.--Nipples, plugs, cap, and bushing.Figure 15-5.--Unions.Figure 15-6.--Flanges.Figure 15-7.--Types of globe valve bodies.BUTTERFLY VALVESSTOP-CHECK VALVESPRESSURE-REDUCING VALVESFigure 15-15.--Pneumatic-pressure-controlled reducing valve for low-temperature service.HYDRAULIC CONTROL VALVESFigure 15-17.--Bucket-type steam trap.Figure 15-19.--Lavatory traps.Figure 15-21.--Basket strainer.PACKING AND GASKET MATERIALSTable 15-2.--Color Codes for Valves and PipingTable 15-3.--Color Codes for Valve HandwheelsFigure 15-23.--Corrugated ribbon packing.Figure 15-25.--Graphite filament yarn.Plain Full-Faced GasketsINSULATION AND CEMENTSFigure 15-27.--Permanent-type insulation of pipe fittings, flanges, and valves.GENERAL CHARACTERISTICS OF FLUIDSPIPING SYSTEM DESIGNDESIGN REQUIREMENTSDESIGN RESTRICTIONSFigure 15-28.--Slip-type expansion joint.COLD SPRING JOINTSFigure 15-31.--Various types of welded joints.PRESTRESSFigure 15-33.--Variable support pipe hangers.Figure 15-34.--Constant-support pipe hangers.Figure 15-35.--Sway braces (single spring design).Figure 15-36.--Symbols used in engineering plans and diagrams.Figure 15-36.--Symbols used in engineering plans and diagrams--Continued.Auxiliary Exhaust SystemWATER SYSTEMSSERVICE STEAM DRAINAGE SYSTEMElectronics Cooling Water SystemFigure 15-37. - Hydraulic control system for operating magazine sprinkling control valves.Drainage SystemFigure 15-39.--Stowage of portable manifold for interim washdown system.HYDRAULIC SYSTEMSGASOLINE SYSTEMSGas Ejecting SystemsSUMMARYPIPING SYSTEM REPAIRSPERMANENT REPAIRSPipe Length ProblemsFigure 16-4.--Bend allowance less than 90 degrees.Table 16-1.--Tangent TableFlange Bolthole LayoutFigure 16-6.--Layout for a seven-hole flange.Table 16-2.--Constant Values for Locating Center of Flange BoltholesFigure 16-8.--Construction of an ellipse.MAKING TEMPLATES AND TARGETSFigure 16-10.--Templates and targets.Figure 16-12.--Portable pipe bender components and assembly.ROTARY PIPE BENDERSPOWER PIPE BENDER SAFETYFigure 16-15.--Bending on a slab.Post Pipe Bending InspectionFigure 16-18.--Flatness limits graph.Figure 16-19.--Pipe cutting, burring, and threading machine.Flanged JointsPlain Flange MakeupFigure 16-22.--Bolt-stud measurements.SWAGE MAINE FITTINGSPipe PreparationPipe Inspection and Insertion MarkingInstallation and InspectionFigure 16-28.--Use of the multipurpose gauge.Figure 16-29.--Proper alignment and fit-up of pipe ends in the coupling.Figure 16-30.--Quality control inspection.Figure 16-31.--Layout for bending tubing in segments.FLARING TUBINGSIZING TUBING AND PIPEJOINING TUBING AND PIPEMaking a Cup BranchGLOBE VALVEFigure 16-42.--Lapping tools.GATE VALVESCHECK VALVESPRESSURE-REDUCING VALVESEXTERNAL PRESERVATION OF VALVESFigure 16-45.--Permanent-type insulation of pipe fittings, flanges, and valves.MISCELLANEOUS REPAIRSREPAIRING STRAINERSMATERIAL REPLACEMENTPROTECTION OF ELECTRICAL EQUIPMENTPREPARATION OF PIPES FOR REPAIREQUIPMENT TAG OUTSEWAGE SYSTEMSSANITATIONDISINFECTANTSHYGIENIC PRACTICESWATCH AND TRAINING REQUIREMENTSCollection ElementTYPES OF CHT SYSTEMSAERATION SUBSYSTEMController, Alarms, and Level SensorsSewage Transfer HosesCHT SYSTEM OPERATIONAL MODESTransit ModeIn-Port ModeFigure 17-4.--Nested ship sewage transfer.SAFETY PRECAUTIONS FOR IN-PORT MODEFigure 17-5.--Submarine tender receiving system.SECURING TENDER RECEIVING OPERATIONSToxic GasesToxic Gases - ContinuedCHT TANK MAINTENANCE NOT REQUIRING TANK ENTRYFigure 17-1.--Comminutor-type CHT system.Figure 17-2.--Aeration subsystem.Figure 17-3.--Strainer-type CHT system.GLOSSARYGLOSSARY - ContinuedGLOSSARY - ContinuedGLOSSARY - ContinuedGLOSSARY - ContinuedGLOSSARY - ContinuedGLOSSARY - ContinuedGLOSSARY - ContinuedGLOSSARY - ContinuedGLOSSARY - Continued
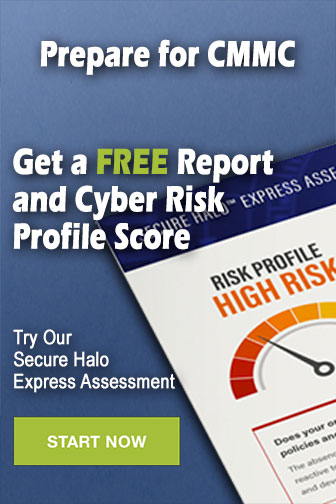